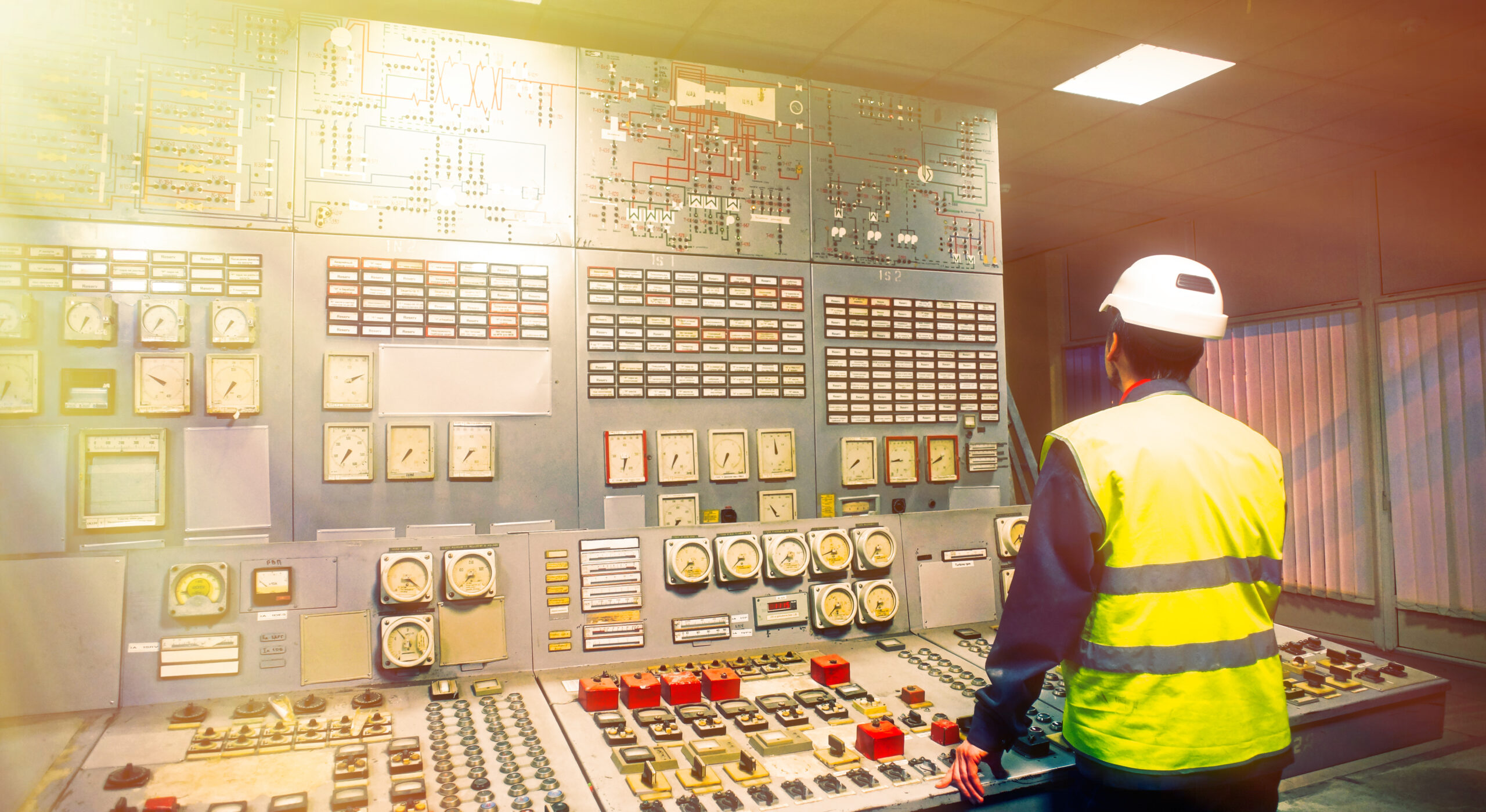
The manufacturing industry is going through a digital transformation to keep up with the evolving market demands. The increasing demand for custom products, shorter delivery times, and the need for greater flexibility in manufacturing processes has led to the adoption of automation technologies. To make the most of these technologies, manufacturers need to leverage software components like Manufacturing Operations Management (MOM) and Supervisory Control and Data Acquisition (SCADA) systems.
SCADA is a control system designed to collect data from industrial equipment. The acronym stands for Supervisory Control and Data Acquisition. It is generally viewed as an architecture combining multiple pieces of software that gather real-time operational (OT) data from sensors monitoring motors, pumps, valves, with multiple hardware collection points such as RTUs (remote terminal units) or PLCs (programmable logic controllers). SCADA aggregates the data to an on-premise server or a remote data server, and enables organizations to use the data for making and deploying data-driven decisions regarding their industrial processes. With SCADA organizations can monitor sites locally or remotely. SCADA includes Human Machine Interface.
MOM, on the other hand, is a broader term that encompasses various software components used in the manufacturing industry to manage and optimize production processes. These components include Manufacturing Execution Software (MES), which is responsible for controlling the order flow between work centers, and Enterprise Resource Planning (ERP) software, which manages resources, orders, and releases.
The integration of SCADA and MOM systems, along with other software components, is critical for maximizing the benefits of automation through software in the manufacturing industry. The integration requires coordination and collaboration among different teams within the organization, as well as the implementation of an MES system that can automate and optimize manufacturing processes. By leveraging the benefits of automation through software, organizations can reduce the risk of human error, improve efficiency, and increase productivity, making them more competitive in an ever-changing global marketplace.
To implement an integrated system for SCADA and MOM, manufacturers often rely on software providers that specialize in automation and data management. These providers offer software solutions that enable organizations to collect and process data from various sources and use it to optimize their manufacturing processes. Some of the key software providers in this space include Rockwell Automation, Siemens, ABB, Wonderware, and GE Digital.
Manufacturers can also benefit from leveraging MES and ERP software to improve their operations. Examples of MES and ERP software providers include SAP, Oracle, Plex Systems, IQMS, and Epicor. By partnering with a reputable software provider, manufacturers can leverage the latest technologies and tools to improve their operations and remain competitive in an ever-changing global marketplace.
One of the key benefits of an MES system is its ability to collect and analyze data from various sources, including SCADA and other software components. This data can be used to improve production processes by identifying areas of inefficiency and optimizing workflows. For example, if an organization identifies a bottleneck in their production line, an MES system can help them identify the cause of the bottleneck and provide data-driven insights to optimize the process and reduce the bottleneck.
Another critical aspect of maximizing automation benefits through software is the ability to provide real-time data and analytics to decision-makers. This enables organizations to make data-driven decisions that improve their overall performance. For example, an organization can use real-time data from SCADA systems to identify equipment that requires maintenance or replacement. This helps them reduce downtime, improve equipment efficiency, and increase overall productivity.
In conclusion, software providers play a critical role in helping manufacturers maximize the benefits of automation through software. They offer a range of solutions for SCADA and MOM, along with other software components, that enable organizations to collect, process, and analyze data from various sources and use it to optimize their manufacturing processes. By partnering with a reputable software provider, manufacturers can leverage the latest technologies and tools to improve their operations
ISA-95 Framework
ISA-95 incorporates the layers model of technology and business process for manufacturing enterprises as levels for the standard. These levels are:
- Level 0 – Defines the actual physical processes and generally is microseconds or milliseconds or smaller depending on the process being measured.
- Level 1 – Defines the activities involved in sensing and manipulating the physical processes. These are generally measured in terms of seconds.
- Level 2 – Defines the activities of monitoring and controlling the physical processes. Typically can be measured in terms of hours and minutes.
- Level 3 – Defines the activities of workflow to produce the desired end products. Typically can be measured in terms of days or hours.
- Level 4 – Defines the business-related activities needed to manage a manufacturing operation. Typically can be measured in terms for weeks or months.
Manufacturing Operations Management systems reside in Level 3 of the model. From a component or software perspective, Levels 1 to 4 can be seen like this:
- Level 1: Intelligent devices such as an Industrial IoT device
- Level 2: Control systems (e.g., Programmable Logic Controllers, Distributed Control Systems, SCADA)
- Level 3: Manufacturing operations systems (e.g., MES)
- Level 4: Business planning and logistics systems (e.g., ERP)
For more information go to www.isa.org