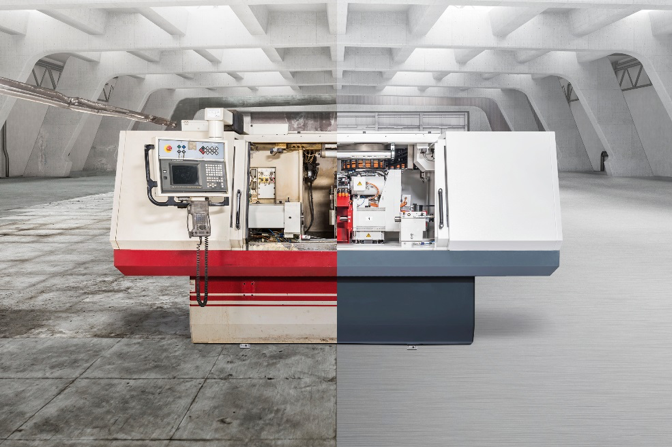
After 14 years in service, a STUDER S40 United Grinding machine that had over 45,000 hours of run time now produces precision components to tolerances it achieved when brand new. The STUDER factory in Switzerland performed the rebuild that involved completely overhauling the machine, and while doing so also provided the machine’s owner LMT Kieninger with a loaner to ensure the customer’s production would continue uninterrupted.
A rebuild, or machine overhaul, makes sense not only economically, but also in the fact that operators continue to run a machine that is familiar to them for a seamless transition after the machine has been rebuilt.
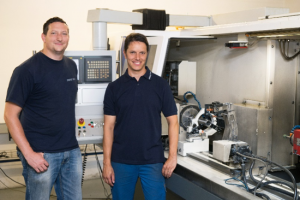
In the STUDER factory, the rebuild specialists disassemble machines down to all their individual parts. The specialists completely refurbish guideways, overhaul the assemblies and replace all worn electrical cabinet components as well as all worn hydraulic and lubricating systems and valves. If spare parts are no longer available, STUDER provides alternative solutions. For the final stages of the rebuild, the casting and components are sand-blasted and receive a fresh coat of paint. Once reassembled, the machine’s geometry is like that of a new machine.
“After our rebuild, we really noticed the difference,” said Heiko Braun, Group Manager of Cylindrical/Surface Grinding and Assembly at LMT Kieninger. “Since the overhaul, we have been grinding with the precision of a new machine. The rebuild process went without a hitch, and the investment has paid off because a 1600-mm grinder is worth its weight in gold for us.”
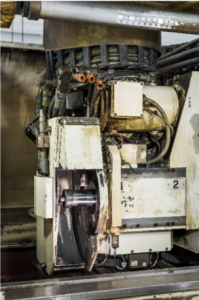
If a customer wishes to expand a machine’s component range, the STUDER overhaul process can also include a retrofit during which a machine is modified to a customer’s particular requirements. This opens up new production possibilities on the same machine, which was the case with Ingold Tools AG.
Ingold Tools had been producing high-precision and complex parts for spindle, compressor, hydraulic and general machine manufacturing with 25 employees since 1946. Among its cylindrical grinders, the shop had an 18-year-old STUDER S21 with two external spindles and continuous fine adjustment of the turret wheelhead (B-axis fine).
STUDER not only updated the S21 with the latest developments, but also retrofitted it to suit the needs of Ingold Tools AG. The cylindrical grinding machine now has an additional internal grinding spindle for internal cylindrical grinding and the relevant fixture for swiveling the tailstock into the park position. The machine also has a new spindle cooling system with its own circuit, as well as a hydraulically swiveling dressing unit. So that all grinding machines have the same mounting, the universal tool headstock was upgraded from MK4 to MK5.
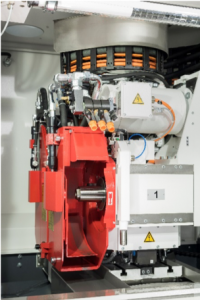
According to Ingold Tools AG’s two managing directors Christoph Jenzer and Edgar Stich, the STUDER retrofit resulted in them getting a second-hand machine with 50 percent new hardware.
About UNITED GRINDING
North America, Inc.
With nearly 200 employees across the U.S., Canada and Mexico and a new 110,000-sq.-ft. headquarters in Miamisburg, Ohio, UNITED GRINDING North America, Inc., strives to increase its customers’ competitiveness through grinding and ultra-precision finishing solutions for the manufacturing industry, backed by single-source customer care. The company’s surface and profile, cylindrical and tool grinding technology groups cultivate a partnership-based relationship throughout the region, selling, automating, rebuilding and supporting precision machines for grinding, eroding, laser ablation, combination machining and measuring under the MÄGERLE, BLOHM, JUNG, STUDER, SCHAUDT, MIKROSA, WALTER and EWAG brands. A subsidiary of the UNITED GRINDING GROUP, the company holds ISO 9001 certification to assure quality in development, production, shipping and support operations. UNITED GRINDING North America, Inc., also holds International Traffic in Arms Regulations (ITAR) Registration.
About UNITED GRINDING Group
With a turnover of around 700 million euros, the UNITED GRINDING Group is one of the world’s leading manufacturers of precision machines for grinding, eroding, lasering, measuring and combination machining. With its eight company brands MÄGERLE, BLOHM, JUNG, STUDER, SCHAUDT, MIKROSA, WALTER and EWAG, UNITED GRINDING offers a broad application knowledge, an extensive product portfolio and a complete array of services on the international market. The Group employs a workforce of around 2500 employees and more than 20 production, service and sales locations and agencies throughout the world.