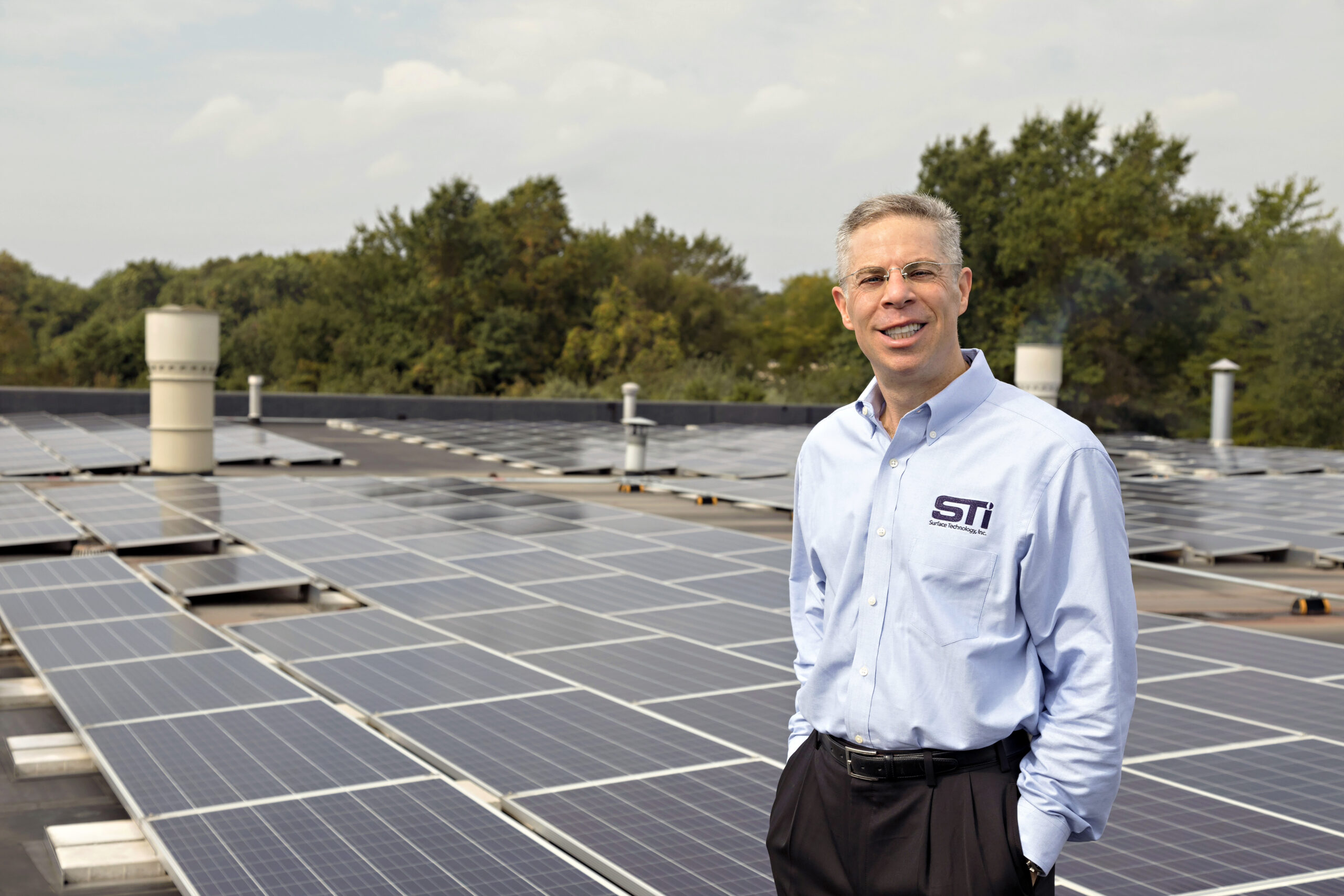
Please tell us about Surface Technology’s work in coating non-metallic products and the advanced coatings themselves that have synergistic properties.
Surface Technology, Inc. (STI) applies our specialty coatings to customers — parts that are made of metals, alloys, and non-metal materials. Our coatings provide important properties including hardness, wear resistance, high friction, low friction, heat transfer, forensic identification. These properties are especially useful in advanced applications, many of which therefore are components made of unique materials. For example, various aerospace components must be lightweight and withstand unusual conditions. Therefore, they are often made of specialty materials including non-metals. Additional examples include medical, food processing, alternative energy, and robotic components which we routinely coat in our facility.
What does “electroless” mean in terms of these coatings?
“Electroless” is a key distinction between our variety of plating and the more generic electroplating form of coating. As the name implies, electroplating is a process that utilizes an electric current and a chemical pass in order to apply a metal coating onto a part. This is very useful in many applications, however it lacks the ability of an electroless plating solution to conform perfectly to even the most complex geometries. So while electroplating may be useful for car bumpers, kitchen faucets, and many other applications where it may be ok for the coating to be thicker on edges and thinner in other areas, the more sophisticated devices on which we apply our coatings require perfect uniformity of thickness of the coating to ensure that the component will operate properly and it’s demanding application. Electroless plating uses a more sophisticated chemical formulation where the nickel metal is deposited onto the part by chemical instead of electrical means. This is why it is so uniform. The electroless plating process is also uniquely suitable for the type of composite plating we specialize in where we incorporate fine particles within the plating to provide synergistic properties and higher performance.
What role does this coating technology play in reliability?
Reliability is a big factor in why our coatings are so useful to end users including manufacturers and machinists that require reliability and performance. Due to the electroless nature of our technology, the coatings are reliable in multiple dimensions. Aside from the uniformity of thickness across even complex geometries, the uniformity of the coating composition is outstanding. For example, the uniformity of fine diamond within the nickel alloy matrix is very evident. These factors allow for consistent performance and extended life of the parts. This is critical to the applications we serve.
Tell us about the other side of the business — the sale of your own in-house chemicals to coating shops.
Our company has pioneered these high-end composite electroless nickel coatings since the 1970s. Therefore, it was not possible to purchase the plating chemicals from any of the existing suppliers in the industry. Their products were made for more generic types of coating, and we needed systems where the chemistry was specifically tailored to work optimally with particles for composite plating. STI developed the core method of using surfactants within the plating bath to make these composite coatings reliable. As demand for our composite technology grew over the subsequent decades, and other plating shops wanted to produce our composite coatings, we were able to supply them with the same chemical products we made for our own use. That started a tradition of our company being a unique supplier in the industry where we supply the most advanced electroless nickel solutions as well as service that is based on our first-hand knowledge of how to best run these processes. This is because we know how to do it in the most environmentally advanced way (we are a zero-discharge facility and all of our electricity is produced by 860 solar panels on our roof) in a location with especially high costs from taxes to labor. We are pleased that plating shops around the world appreciate the unprecedented support we can give them when they run our processes. A very exciting update on our chemical solutions is that in recent years, STI has invented, developed and commercialized the greatest breakthrough in electroless nickel plating. Very simply, for decades all electroless nickel plating worldwide required three different chemical solutions to make and operate the plating bath. We invented “One-Plate” which is just a single solution that replaces the traditional three solutions. One-Plate is a drop-in solution that allows plating shops to experience benefits in cost savings, higher productivity, less labor time, more consistent quality, less waste, easier stocking, and many other advantages. Whereas our composite electroless nickel chemical products have been for specialized uses over the years, One-Plate is being adopted by the broader plating market at a rapid pace.
Can you tell us about the contract R&D side of this business? Are you working on any exciting projects?
The entire team at Surface Technology is indeed proud to continue the tradition of innovation established by my father who was recently honored posthumously with induction into the Plating Hall of Fame. This spirit of innovation is alive in everything we do from our basic operating systems, continual improvement, and rewarding novel any member of the team for ideas that improve quality, productivity, or new concepts. This award is appropriately named, The Dr. Nathan Feldstein Award. And the innovative principle is very much a factor in our R&D activities. As companies, universities, national laboratories, etc recognize our expertise in surface finishing, we are routinely approached to provide custom R&D services to solve their needs. These projects are always very interesting. Recently, a number of these contract R&D projects have been involved in exciting areas such as military applications, 3D printed components, aerospace including outer space devices, and providing higher friction surfaces for medical, dental, robotics, and wind energy applications.
Tell me more about your thoughts behind being this tech company with “outstanding production and chemical capabilities.”
We have in fact reaffirmed this commitment since I expressed that sentiment previously. When we invented One-Plate and knew it was the most innovative product in electroless nickel in decades, we certainly reconsidered if we should take on more of a sales and marketing focus. But it was an easy decision to expand, not change, our core focus on technology and manufacturing. So we have expanded our network of distributors around the world that are now selling One-Plate in 20 countries on 5 continents. We work very closely to support them and of course learn from them as well. These distributors have unprecedented knowledge in their markets and relationships. The One-Plate suppliers of North America are even banding together to sponsor the electroless nickel EN 2022 Conference in October.
Are there any new products we should know about?
While One-Plate is useful for general electroless nickel plating, it is also usable for composite electroless nickel plating. The most exciting example of this is with electroless nickel-PTFE (Teflon). This is a coating that has been used globally for decades because nickel-PTFE coatings are hard, wear resistant, corrosion resistant, and have a very low coefficient of friction thanks to the PTFE. STI has always been the leader in formulating the specialty PTFE dispersions used in the process. The One-Plate nickel-PTFE version we have developed vastly surpasses all previous generations of such coating systems. Ours has all the benefits of being just a single component as noted above, and in addition, ours is the most environmentally advanced ever. One-Plate with PTFE has the longest bath life, lowest metal concentration (meaning less waste), no heavy metals, no PFOA, PFOS, and not even any fluorinated surfactants. So it performs the best, is the cheapest to use, and even surpasses regulatory requirements.
How has the COVID-19 pandemic affected your business?
STI was proud to have never missed a day of work producing products for our customers during the pandemic. Our company was deemed a crucial manufacturer and therefore allowed to continue our operations. In fact, we were able to serve (and continue to serve) many new customers who were unable to get their critical parts coated by other suppliers that were not operating. Our team is especially gratified to do the high precision coating required on components used in the freezers required to store the Covid-19 vaccines. The pandemic also provided a substantial boost to our chemical solution sales. The reason for this is that the simplicity of ordering, stocking and using our One-Plate electroless nickel has been even more beneficial in the challenging time of the pandemic, inflation, labor shortages and supply chain problems. Only needing the single One-Plate component makes it easier for plating shops to order and stock easier, produce with fewer and often less experienced workers, and maintain productivity and quality.
What’s on the horizon for Surface Technology?
STI is growing at a fantastic pace in all areas of our activities from chemical sales to plating services to R&D. Fortunately, there are many opportunities in the works to expand these products and services in current and exciting new industries. Our company is also engaged with Trion Coatings https://trioncoatings.com/ to develop and bring to market a product called SAFE Chrome which is the practical chrome plating solution the industry has been looking for to avoid the environmental and health problems inherent with traditional hexavalent chrome plating.
Michael Feldstein is the President and Director of Innovation, Surface Technology, Inc. Learn more about the company at www.surfacetechnology.com.