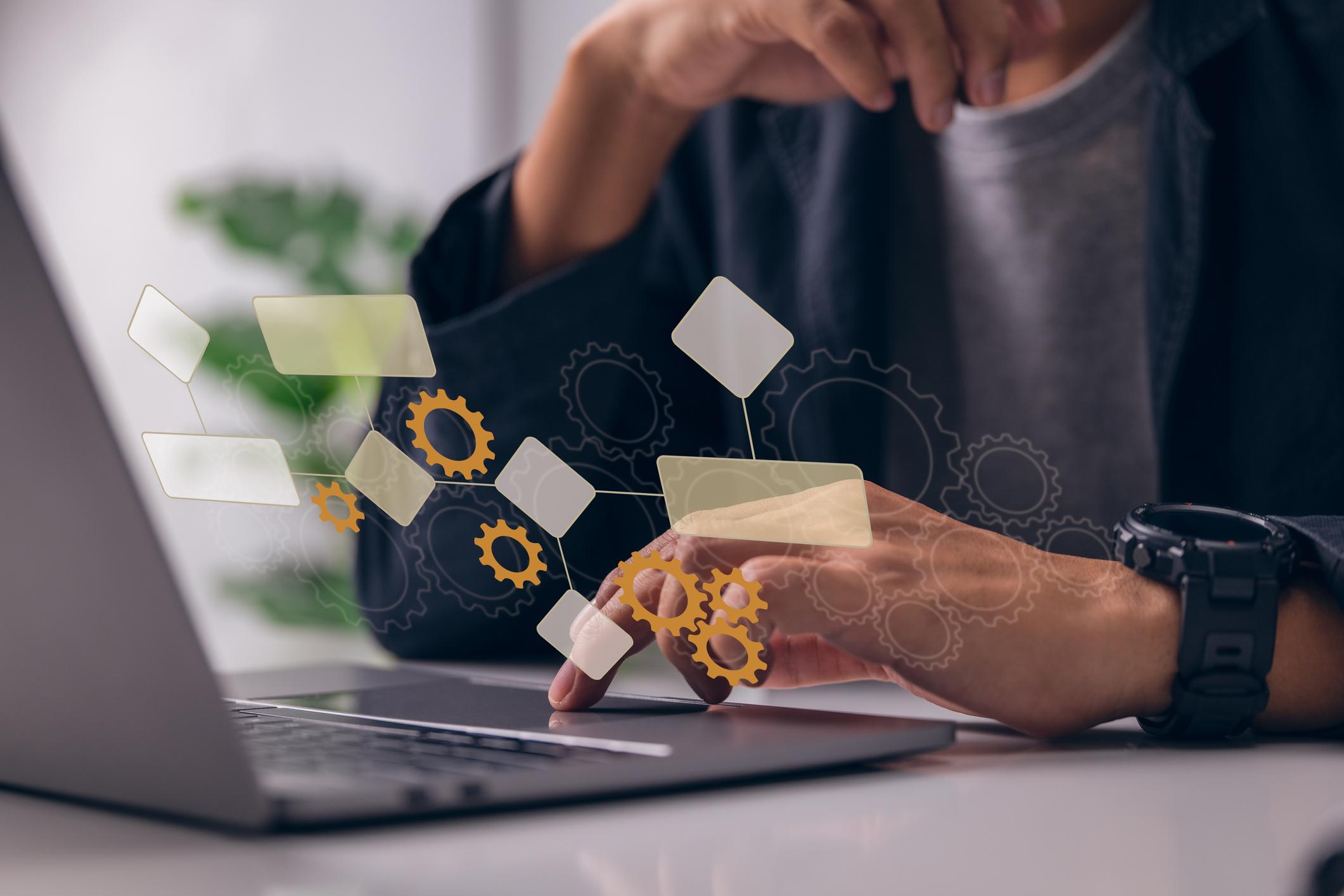
Increasingly complicated configuration workflows with a growing number of rules, dependencies and variants are a challenge for manufacturers today. This heightens the need for building and improving product models, as well as conducting thorough evaluations of all viable configurations and rule dependencies in a product model.
There is a demand for more sophisticated configuration technologies as a result of the rising pressure on existing configuration processes. It’s essential to comprehend the various technologies and what configuration solutions are capable of if you want to convince customers that everything you sell can actually be built.
What manufacturers are up against
Products are becoming more complex. There are millions of different possible configurations of a certain product in some businesses. Every one of these configurations has a unique set of details, including its price, documentation, CAD drawings and a Bill of Materials (BoM).
Manufacturers are attempting to control all these various configurations and make sure that they are only providing customers with options that are truly available. It is quite challenging to maintain everything in a coherent, understandable and visible way across many functions.
But managing the complexity of configurable products is not just about the physical product. It involves managing software aspects as well as aftermarket/servicing. Introducing software into products causes several issues, not all of which can be addressed using a configuration solution. For example, the software development cycle/versioning can be difficult to align with the traditional lifecycle of physical products as managed in a product life cycle management (PLM) system.
However, a configuration system can ensure that software parameters that needs to be set when deploying the product are set according to the requirements specified as part of the configuration process. Identifying and configuring a particular product in the point-of-sale can also generate the configuration parameters that need to be set when the product is commissioned. A configuration system is also central when replacing parts or upgrading an existing machine with new capabilities, such as understanding how the machine was configured. This is a better starting point than understanding the parts-content of the machine.
Combination overwhelm
Many businesses are working with enterprise resource planning (ERP) systems to try to address this on the manufacturing side. Most engineering departments use a PLM system of some kind. Both circumstances entail writing rules and testing out scenarios for particular configurations.
An automobile manufacturer might wonder, “What happens if I choose this variant, and I choose that size and this color?” They’ll receive a path that outlines their options and illustrates how a consumer might navigate this path. But there isn’t any meaningful analysis being done.
Trial and error is neither viable nor sustainable when working with, for example, several hundred parameters. To cover more than a small portion of the potential combinations would take too much time and effort.
Most businesses in this position are left with no choice but to test a small number of probable outcomes and hope that will suffice – but issues could arise. Because of a rule change that unintentionally disabled the French market, for example, customers of one company couldn’t order cars in France. The organization then had to spend time reviewing the incident and determining the cause. They found the cause and fixed it, but not in a strategic way.
Managing the complete product
In the ERP world, there’s the concept of Configuration Items (CIs), which is any item, service or other element that needs to be managed in order to ensure successful delivery of a service. As products and services become more sophisticated in meeting customer demands, as well as new business models like servitization and subscriptions, the number of software, service and other CIs that aren’t part of the core increases. For example, ensuring that the right software versions are delivered together with hardware, that the correct service and support plans are included. Increasingly, the analytics capabilities need to be included to ensure that customer KPIs are being met.
All of these items need to be considered part of the extended product model and managed as part of the configuration. Fortunately, the same concepts and rules can be applied to ensure that the right CIs are included in each customer delivery and managed across the lifecycle of the customer solution.
Working with configuration technology
What if there was a way to create and analyze viable configurations in a much more comprehensive manner without wasting many employee hours on trial and error? What if everything could be carried out in a far more organized and centralized way?
With a configuration solution, it allows the ability to look at the individual rules, figure out how they affect each other, and then figure out what combinations are possible. This method may also assist in discovering other intriguing data. An engineer may discover, for example, that not all expected combinations of engines and transmissions are allowed by the configuration rules.
The important thing, though, is that it helps identify these restrictions and exceptions before buyers can. This avoids situations in which a customer chooses a specific configuration, only to find out from the engineering department that it isn’t feasible, forcing the sales representative to break the bad news to the customer.
A configuration solution enables a manufacturer to validate the BOM, ensuring that the “recipe” of parts is complete for whatever configuration is received from the sales team. BOM errors are easy to make and might be problematic for some configurations. And you might not be aware of this until you get to the manufacturing facility.
The outcome is that data is verified before sharing it, providing peace of mind that what an organization is providing is accurate – and internal stakeholders can identify rule flaws before customers do. A configuration tool also enables the ability to optimize and evaluate the potential options that customers are likely to select. Although most businesses have not yet reached this level of maturity, it would help eliminate some complexity by, for example, bundling choices.
The configuration model provides information about all valid configurations. If the model is combined with take-rates for each option in the configurator, organizations can calculate the probability of each part number in the BOM to be selected, allowing engineering to “cut the long tail” – basically eliminating those combinations that are unlikely to be selected and thus saving parts. But there can be reasons for keeping combinations around that rarely sell. For example, many automotive manufacturers keep base models available to offer a low starting price, though almost all customers select upgraded versions.
These capabilities are not only relevant to the core product, but to all the additional configuration items that need to be included to ensure that delivery to the customer is successful. The same optimization process can be applied enabling efficient management of all configuration items.
Configuration management: Mastering the possibilities
The configurability possibilities available in manufacturing today are far too complicated for manual, error-prone workflows. To minimize errors and duplicated work, all departments—engineering, production, sales and service—must collaborate from a single source of data truth. Understanding the numerous capabilities and opportunities that configuration solutions provide is crucial for making sure that everything you offer for sale can be produced and be profitable. With the use of configuration technology, manufacturers can generate valid configurations more quickly and precisely.
By: Henrik Hulgaard, cofounder and vice president of product management, Configit