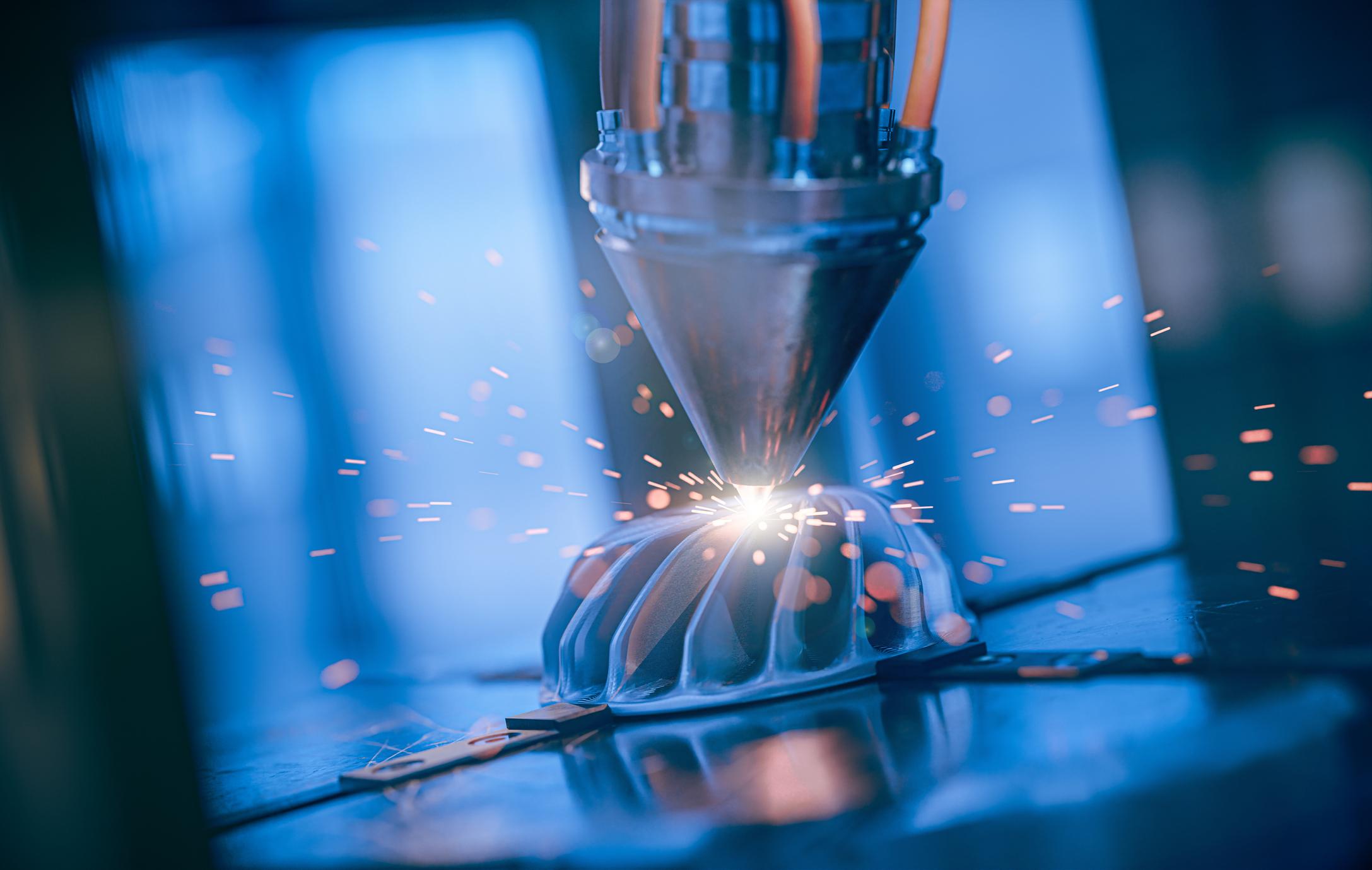
Nearly a year ago, on Tuesday, October 18, 2022 General Motors released a hype marketing press article entitled “Cadillac CELESTIQ Establishes New Standard of Automotive Luxury.” The byline said that the Cadillac CELESTIQ was going to be the most technologically advanced Cadillac ever and is designed to be the world’s first all-electric ultra-luxury sedan utilizing innovative technology in the service of personalized, handcrafted artistry. GM further goes on to say that “This unique and individualized experience is augmented by Cadillac’s global leadership in electrification, available hands-free driver assistance technology and connected services. CELESTIQ sets the benchmark for handcrafted, multisensory and immersive EV luxury experiences.
‘CELESTIQ is like no Cadillac before it and the client experience is equally exceptional,” said Global Vice President of Cadillac Rory Harvey. ‘Each vehicle is a unique expression of its owner, leveraging leading-edge technologies that make the driving experience personal and rewarding.’ Harvey previously in the press release stated that the CELESTIQ will be ‘a completely bespoke work of automotive art, built around the most advanced and innovative technology that we [GM] have ever engineered into an automobile.’
This is very heady stuff indeed. Among the other highlights was something very interesting and relevant to our theme this month. GM specifically calls out additive manufacturing (AM) as one of the innovative technologies used on the vehicle. Specifically with “115 3D printed parts in the production vehicle, the CELESTIQ demonstrates GM’s broadest use of this process.” Some of the items which are 3D printed include the steering wheel center, touted as the largest metal 3D printed part GM has in production, and the seat belt adjustable guide loop which was at the time GM’s first safety-related 3D printed part. Other 3D printed parts on the vehicle are window switches, grab handles, console decor and structural pieces under the vehicle’s surface. GM’s press release says that, “The use of 3D printing and additive manufacturing is cutting-edge technology that produces several important CELESTIQ design elements, such as the steering wheel décor, which would be impossible to create with typical metal castings and CNC milling.” Here is the catch though – this vehicle, headed into production in December of 2023, will have an MSRP expected to be north of $300k. They will only be produced as they are personally commissioned by their owners. OK, so we have AM being touted on an on-demand production line for a low volume produced, high-end EV. Ok, so how soon before application of AM on mass production lines? Is it ready for “prime time?” Let’s take a broader look at the technologies.
Seven Types of Additive Manufacturing
3D printing is additive manufacturing. However, all additive manufacturing is not 3D printing. Back in February, we discussed additive manufacturing in one of our 3D printing articles. However, we took a very narrow view in our example, only discussing powder bed fusion techniques. Our base definition of adding material driven from a digital definition of the layer, and fusing it is still a good basis for discussion. However, the ASTM Committee F42 on Additive Manufacturing Technologies publishes the official terminology standard for the industry, and with this terminology also extolls the technology advancements that have moved beyond simply 3D printing. ASTM F2792-12a generically defines seven process classifications for additive manufacturing, specifically material extrusion, sheet lamination, binder jetting, material jetting, directed energy deposition, powder bed fusion, and vat photopolymerization.
MATERIAL EXTRUSION
Material extrusion is an additive manufacturing technique in which thermoplastic material is pushed through a heated extrusion nozzle and deposited layer by layer to build an object.
Fused filament fabrication (FFF), also referred to as fused deposition modeling (FDM), is the most commonly used additive material extrusion process. FDM was developed by S. Scott Crump in the late 1980s and was commercialized in 1990.
In the FDM process, a heated extrusion head precisely lays thermoplastic material over the print bed according to 3D CAD (computer-aided design) data. The build platform then lowers by a thickness of one layer and the next layer of material is applied. Layers solidify and fuse together as they cool down, thus building the part. The completed part is removed from the print bed and support materials are cleaned. Post-processing is performed to produce a smooth surface finish.
Various polymers for the filament can be used, including acrylonitrile butadiene styrene (ABS), polycarbonate (PC), polylactic acid (PLA), high-density polyethylene (HDPE), PC/ABS, and polyphenylsulfone (PPSU). ABS and PLA have a high heat resistance and an excellent strength-to-weight ratio making them applicable in many Industrial-grade projects. Multiple projects in the open-source community exist that are aimed at processing post-consumer plastic waste into filament. These involve machines to shred and extrude the plastic material into filament.
FDM has some restrictions on the shapes that may be fabricated. For example, FDM usually requires a support structure for over-hanging geometries which can be broken away during finishing. FDM is used in a number of industries, including aerospace, automotive, and medical, to produce functional and durable prototypes and parts.
The Studio System 2 from Desktop Metal is an example of an additive manufacturing system that uses high pressure metal extrusion technology.
SHEET LAMINATION
Sheet lamination, also called laminated object manufacturing (LOM), is a rapid prototyping process in which sheets of material are joined together to create an object. The sheets can be rolls of paper or even metal. Originally paper was the primary material, and it is commonly used for durable 3D objects with complex geometries. The process is fairly straightforward. Imagine a roll of paper feeding to a waste roller, and moving across a build surface. A bonding material is applied to the paper, which hardens the material or provides an adhesive for the next layer. The initial paper is cut with a laser or knife, then the build surface is lowered. The waste is rolled on to a second roller while pulling the new layer of building material across the build surface, or print bed. The process is completed based on the 3D information delivered from the CAD system to the sheet lamination machine. You can imagine how metals or even composite materials would work in this machine. Ultrasonic additive manufacturing (UAM) is a type of sheet lamination process that uses principles of ultrasonic welding to produce metal parts. It uses CAD data to ultrasonically bind layers of metal sheets to metal substrate surfaces. Generally, a bonding adhesive is used to join paper sheets, whereas this moderate force and high-frequency vibratory energy are required to create metal parts.
Fabrisonic is a 3D service provider that touts the sheet lamination approach, and provides innovative 3D metal printing services for aerospace metals, aluminum and copper. They use the low-temperature ultrasonic additive manufacturing (UAM) technology. – with no melting of metal.
BINDER JETTING
Binder jetting, also known as drop-on-power printing, is a 3D printing process that creates solid objects using a 3D CAD file. It works with a variety of materials, including ceramics, composites, sand, and plastics. The binder jetting process was developed by MIT professors Dr. Emanuel Sachs and Dr. Michael Cima in the late 1980’s, with their patent being published in 1993. MIT licensed this technology to a number of companies, including Z Corporation. Z Corporation was later acquired by 3D Systems in 2012.
In binder jetting, the process uses a modified version of the inkjet printing process, therefore not requiring a heat source to bind the materials. A building material is applied to the print bed. Next, the print head selectively binds the build material according to the part’s 3D CAD data, using a binding agent such as glue. Some machines can have as many as 5 print heads. The build platform is then lowered by the thickness of a single layer. This process is repeated, connecting the layers of powder into a finished part. The end result is a cube of power with a number of solid parts inside. These parts must be excavated from the cube of powder and post-processed with an air compressor to remove any residual powder. In some cases, a heat treatment is also used in the post-processing. Any unused powder can often be used again.
A provider in this space is Desktop Metal. In less than a decade in binder jetting, Desktop Metal has a growing team of 1000+ employees, and is now one of the world leaders in binder jet 3D printing, Desktop Metal’s technologies work with metals, sand, wood, polymers, and ceramics and composites, including carbon fiber and soon fiberglass (in active R&D on their website).
MATERIAL JETTING
Material jetting is a full-color additive manufacturing technique in which droplets of thermoplastic are selectively deposited using drop on demand (DOD) technology, similar to how an inkjet printer dispenses individual ink drops only when needed. In material jetting, the print head is not heated to bind the material. Instead, an ultraviolet (UV) light source is used to cure the liquid resin.
The print head deposits a layer of liquid photopolymer resin on the print bed. A UV source moves over the deposited layer, polymerizing the build material. The build platform then moves down by the thickness of one layer, and another layer of material is added over the previous layer. This process repeats until the entire 3D object is finished. This differs from the binder jetting process as the build material itself is dispersed versus an adhesive. This also differs from fused deposition modeling as only drops of material are jetted versus strands. Post-processing is usually required and consists of removing support material with a water-jet.
3D Systems, HP, and Vader are a few of the industrial equipment providers for this technology.
DIRECTED ENERGY DEPOSITION
Directed energy deposition (DED) is an additive manufacturing process that uses a heat source, such as a laser or electron beam, to melt metal powder or wire. Parts are created by melting material and placing it where it is needed. It is commonly used to repair or add additional features to existing parts. Feedstock material, usually metal powder or metal wire, is fed through a nozzle, and an energy source is introduced to create a melt pool. Generally this energy source is a laser or arc weld or an electron beam. This melted metal pool is then “directed” on the surface, leaving behind a wake of molten material that solidifies.
Prima Additive is a company that provides machinery for this type of process using cobalt chrome, copper, and steel alloys.
POWDER BED FUSION
Powder bed fusion (PBF) is an additive manufacturing technology that uses a heat source, such as an electron or laser beam, to melt and join material powder to create three-dimensional objects. This technique can be used to create both plastic and metal parts.
There are four types of powder bed fusion processes depending on the source of heat used. Direct metal laser sintering (DMLS), selective laser sintering (SLS), and selective laser melting (SLM) use laser fusion, electron beam melting (EBM) uses electronic beam fusion, multijet fusion uses agent and energy fusion, and selective heat sintering (SHS) uses thermal fusion. A thin layer of powdered material is spread over the overbuild stage. Next, the PBF machine applies a heat source to selectively scan over and fuse the powder into a first cross-section of the part using the 3D CAD data. The build platform is then lowered by the thickness, and a new layer of powdered material is spread on the previously deposited layer. This process is repeated over and over again until the entire part is created. Support structures are not required in PBF processes. The printed part is simply removed from the build platform and cleaned to undergo post-processing.
GE Additive, 3D Systems, Velo3D, Trumpf, Renishaw and AddUp (a joint venture between Michelin and Fives) are players in providing technology or services in this space. Prima Additive is also a provider of machinery for this process, providing solutions for aluminum, copper, steel and nickel alloys.
VAT PHOTOPOLYMERIZATION
Vat polymerization is an additive manufacturing process that uses a vat, or container, filled with photosensitive liquid resin and a light source to create solid objects.The build platform lowers from the top of the tank filled with liquid polymer. An ultraviolet light source selectively cures liquid resin according to the pattern defined in the 3D CAD data file. Upon contact with the light source, the photopolymer undergoes a chemical reaction and solidifies. This process is known as photopolymerization. The build platform then lowers by one layer height and more resin flows over the top of the print bed. A sweeper blade moves over the previous layer to ensure that a thin coat of liquid resin is spread out evenly on the surface. This process is repeated layer-by-layer until the part is finished. The printed part is then removed from the resin and from the build platform. It is then submerged in a chemical bath that washes away excess resin and cured in a UV oven to increase its stability and strength. At this point, any support materials are removed from the printed part.
Vat polymerization is a broad class, encompassing a number of 3D printing technologies, including stereolithography (SLA), digital light processing (DLP), and continuous liquid interface printing (CLIP™). CLIP™ is a new process that has been developed by a startup company called Carbon. The process is much like using a photomask in the silicon industry to focus on a silicon dioxide substrate. In CLIP™ a mask is placed in front of a UV light shining up on a transparent vat containing a light activated resin. The UV pattern causes the resin to harden on the build surface, which is raised one layer of height and another mask used to shine a new UV pattern. As the build surface is being raised the part is being printed one layer at a time from bottom to top. Each time the build surface raises, more resin enters the lower area – and creates an oxygen barrier in the bottom of the reactant tank. This barrier is known as a dead zone, and eliminates any reactions in the very bottom of the tank against the window. After the final layer is hardened, a heat based post-process is performed.
Industries Using Additive Manufacturing
LuxCreo is a 3D printing provider of both services and technology. On their website they list seven key industries using additive manufacturing. These include dental, medical, footwear, aerospace, energy, consumer goods and automotive.
There is a common theme in all of the additive manufacturing technologies – improved strength to weight ratio. As complex geometries, that can more easily distribute and support forces and that can more effectively distribute stress and strain, continue to evolve in their design – using lattices, helixes, and other imaginative approaches, additive manufacturing will continue to pick up steam.
At the moment, it seems that Fortune 500 companies, and even government driven entities such as NASA have created critical mass. NASA announced in March of this year that out of its two new Space Technology Research Institutes (STRIs), one will be dedicated entirely to the understanding and rapid certification of metal parts made using additive manufacturing technologies. Behemoths in the auto industry are using additive manufacturing to remove weight from electric vehicles – a top of mind necessity due to the added weight from battery infrastructure on the EVs. Not only will electric vehicles and space vehicles continue to drive the industry, but so will advances in medical applications (for example prosthetics which are designed exclusively for an individual patient) and higher efficiency power turbines. Names like GM, Ford, GE, and Boeing continue to be associated with advancements in additive manufacturing, in most cases have a business or unit dedicated to building and deploying applications of the technology.
AM is around us already and the biggest companies in the world are using it. All the research we found forecasts a higher than 20% CAGR through 2030. Prime time process? You bet.