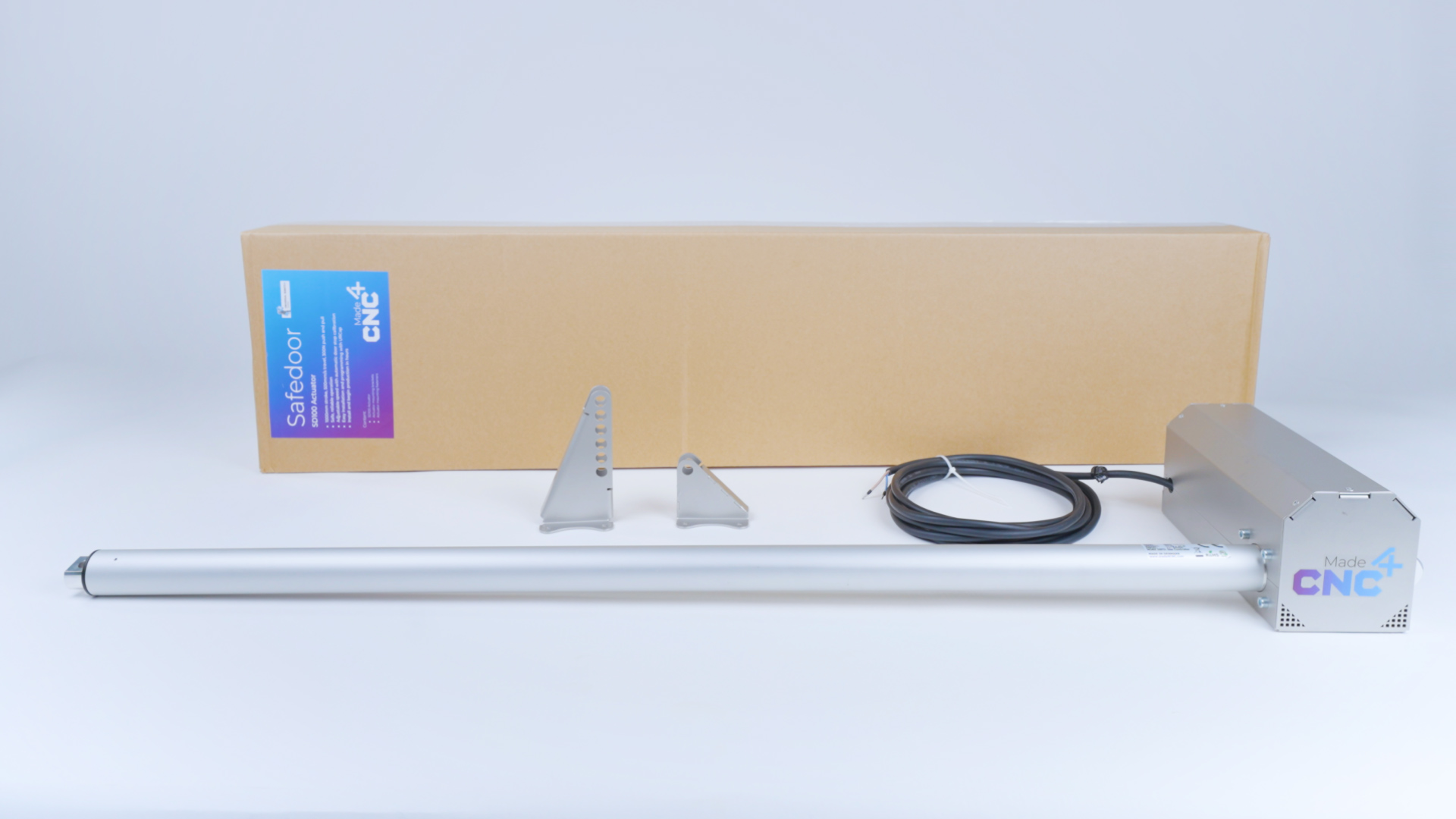
In a recent interview, Madsen explained the game-changing benefits of the Safedoor SD100 system and talked about Made4CNC’s ties to the renowned Danish collaborative robotics sector, coping with supply chain stresses, and why Denmark has become such a hotbed of innovation.
What is the Safedoor SD100?
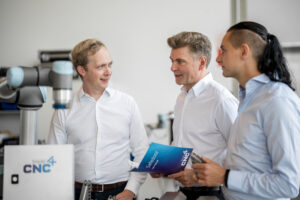
The Safedoor D100 is a complete solution for automating CNC machine door opening and closing. Its main hardware component is a box that’s easy to mount above the door of your existing CNC machine.
Inside the box, a linear actuator provides the force required to open and close CNC machine doors. The Safedoor SD100’s linear actuator design helps to ensure consistent, durable, and safe operation. With a linear actuator, forces are confined within the actuator itself. Alternative systems require external forces to keep the belt tense and the pulleys must be mounted on some sort of beam. The Safedoor 100’s linear actuator design eliminates these concerns which are commonly found in traditional, non-electric, DIY solutions.
The SD100’s intelligent Safedoor Controller monitors all aspects of the door motion, ensuring smooth and reliable operation.
What problem does it solve?
The Safedoor SD100 is an easy-to-use solution to a long-standing component feeding challenge in machine tending automation. Most of the world’s CNC machine applications require either an operator or a robot arm to physically open and close the machines’ heavy doors every few minutes. In fact, despite the increasing proliferation of automated solutions across all sorts of industrial applications, only a tiny fraction of the world’s CNC machines are automatically fed components. That’s a missed opportunity.
Prior to the launch of the SD100, machine shops that wanted to increase production and throughput on machine tending applications faced some stark choices: upgrade their legacy CNC machines, invest in a new CNC machine, or develop an ad hoc, ‘DIY’ solution. CNC machines cost hundreds of thousands of dollars. The Safedoor SD100 costs between USD $4,000 and $6,000, so the financial upside is clear.
The benefits of the SD100 aren’t limited to that upfront capital cost savings.
DIY door opening solutions typically incorporate pneumatic cylinders, which present a wide range of potential safety hazards. In addition, because they are neither standardized nor tested, DIY solutions force integrators and in-house engineers to build everything from the ground up, including custom brackets and enclosures. This slows deployment and introduces unnecessary layers of complexity and risk to the overall application.
The fully electric Safedoor SD100 eliminates these problems. It is standardized, fully tested, and proven in the field. Moreover, with safety in mind, the SD100’s software package allows users to adjust the speed of the CNC door, making risk assessments easier to conduct. The product comes with all the hardware, software, and wiring you need to boost machine tending productivity quickly.
What CNC machines and robot arms does the Safedoor SD100 work with?
The SD100 can handle doors that are up to 1 meter wide and weigh 400 kg, at a speed of 500 mm/s. It’s easy to deploy a system that can connect to any robot and CNC machine via galvanic insulated digital inputs and outputs. For extra integration, we have developed plugins for cobots from Universal Robots and Omron. These plugins are fully integrated on the hardware and software sides and you can access the Safedoor SD100’s intuitive programming interface directly from your existing cobot pendant. We plan to roll out more plugins this year for other robot brands.
How do you deploy it?
To deploy the SD100, all you really need to do is mount two brackets – one on the fixed frame and one on the door. Next, put the actuator in between and you are done with the mechanical integration. The SD100 is typically up and running in a few hours.
This is all good for productivity and throughput. It’s convenient for customers and it saves integrators time and money. For example, one of our customers has moved from 16 hours of machine tending per day to 24 hours, because the SD100 enabled full automation of key component feeding processes. That kind of throughput boost can have a phenomenal impact on companies’ bottom lines.
The system is also good for existing workers who appreciate not having to perform the same tedious, unergonomic door opening and closing tasks all day. So, it’s a win-win-win for the manufacturers, workers, and robotics integrators.
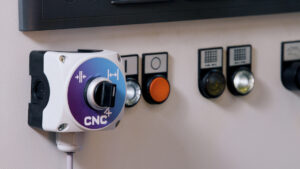
Can the Safedoor SD100 be deployed without a robot?
Yes. Quite a few of our customers are attracted to the ergonomic aspect of the system. They have a worker take pieces in and out, but the SD100 takes over the repetitive, physically draining door opening and closing part of the process. If deployed without a robot, the operator simply has to twist a knob and the CNC machine door will open/close as requested.
How is Made4CNC coping with the current global supply chain crisis?
The uncertainty around the supply chain is a classic double-edged sword from Made4CNC’s perspective. On one side, it has been more of a hassle to get parts, from drive components to chips used in the controller and even cardboard. We’ve spent a lot of time sourcing cardboard.
But we have some great suppliers and they have really leaned in on their side, and together we managed to pull through it. We have stock. And will be able to have stock going forward.
On the other side, we have found that the current materials shortage is a great opportunity for a lot of suppliers to introduce automation. When you can’t get the part you ordered from China, or the shipping and transport rates are too high, it drives companies to bring production at least one step closer to their backyard.
In turn, this drives all types of automation adoption, including automation of CNC machine tending. So, in that sense, the supply chain problem is a positive for our business, because our solution helps companies make that transition from manual to automated processes.
2021 was a pretty bad time to launch in some respects, but a good time in others.
Made4CNC’s executive team has close ties to the world-renowned Danish collaborative robotics sector and the company HQ is in Odense, a noted cluster for collaborative robotics innovation. What is the significance of this, both for Made4CNC and its customers?
Our founders have extensive experience in collaborative automation. Thomas Visti, helped pioneer the cobot concept as the first CCO at Universal Robots (UR) before becoming CEO of Mobile Industrial Robots. Lasse Kieffer and I both worked at UR in our first engineering roles and later founded Purple Robotics acquired by OnRobot. Between the three of us, we have extensive experience in disrupting traditional automation.
Cobots address key problems around the costs and complexities of traditional industrial automation. Cobots are easier to use, safe to deploy around humans following a risk assessment and have a much smaller footprint than traditional robots. Cobots provide levels of flexibility, speed of deployment, safety, usability, and fast ROI that traditional cannot compete with. Cobots are robots that everyday people can use –not just robotics PhDs. Cobots make for user-friendly experiences.
Made4CNC has the same thought train on easy integration, easy usage, and safety that the leading cobots and lightweight industrial robots are known for.
What makes Denmark such a center for automation innovation?
That’s hard to say as a Dane. But we are free thinkers, we don’t care too much about hierarchy, and people are safe to speak their minds. This produces a culture that supports thinking differently and trying new ideas out. These factors lead to innovation, as we have seen with the worldwide success of collaborative robotics and new automation solutions like the Safedoor SD100.
What’s next for Made4CNC?
The overall goal of Made4CNC is to make machine tending with robots as easy as possible. Besides releasing additional specialist plugins for leading robot brands, we’re also looking into ways that we can simplify connectivity between the robot and the CNC machine and exploring technologies that make machine tending safer, easier, and more reliable.
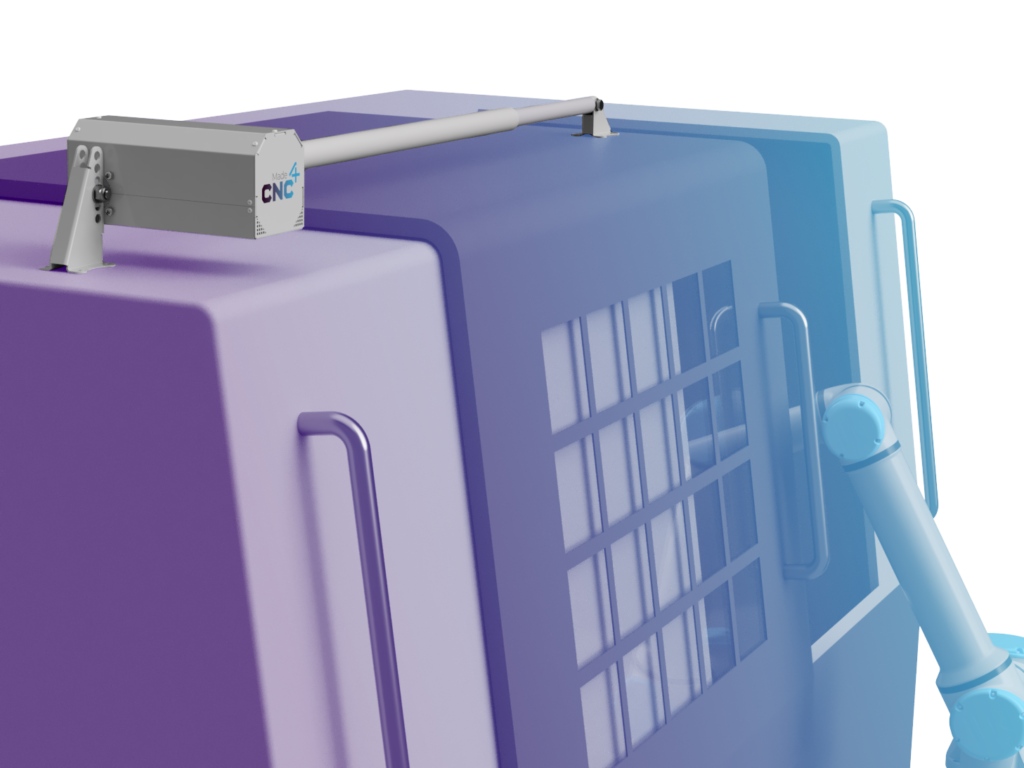