When the OTTOSTAHL GmbH had to replace an old rotary table shot blast machine, the company insisted on short cycle times, high energy efficiency and relieving the personnel from strenuous and monotonous physical activities. These challenging demands were met by Rösler and the automation specialist Teqram with the universally usable rotary table Easy Shotblaster RDT 150, equipped with a stationary “intelligent” robot. This robot places the work pieces on the rotary table in a manner that optimally utilizes the entire table area without requiring any “teaching” operation.
OTTOSTAHL produces up to 30 mm thick, highly precise plasma-cut and up to 300 mm thick flame-cut components. The company’s service portfolio includes the customized production of the components with CAD technology and detailed work plans for the respective manufacturing method. Furthermore, post-processing operations such as shot blasting, drilling, mechanical chamfering as well as arranging material testing through independent external material testing offices are also offered by the company. An inventory of 4,000 tons of different steel grades and qualities, combined with a proven supplier and partner network, guarantees quick and reliable order processing.
A major factor for the investment – the shortage of skilled workers!
In its shot blasting department for sheet metal components the company is utilizing three machines (two continuous flow roller conveyor machines with an operating width of 3,800 mm and a rotary table blast machine). After it had been used for more than 60 years, the old rotary table blast machine was replaced by a RDT 150 system from Rösler. Key customer demands for the new system were the achievement of the specified shot blast results for a broad range of different components, short cycle times and high energy efficiency of the entire system. Since it is very difficult to find qualified workers in Magdeburg, the company also demanded that the existing personnel be relieved from strenuous physical activities. Therefore, the fully automatic mechanical handling of the components was also a key requirement. Based on these specifications Rösler and Teqram developed a fully automatic shot blasting solution around the Easy Shotblaster RDT 150 rotary table machine. The entire blast system is integrated into a manufacturing cell measuring eight-by-eight meters and consists of an intelligent stationary robot and the RDT 150 shot blast machine equipped with suitable accessories.
Robot recognizes the components without the requirement for “teaching”
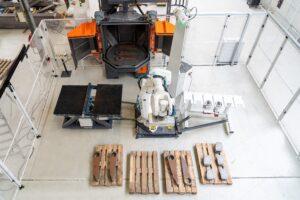
With its innovative image processing technology the vision-controlled robot, with a load capacity of up to 200 kg, automatically recognizes the components placed into its working section, completely independent from their position on the pallet. This eliminates the normally required time-consuming teaching or programming of the robot. Moreover, with the intuitive interface no special knowledge is required.
After the automatic selection of a suitable gripper from the gripper magazine the robot picks up the components and places them on the rotary table in optimum position. Then it provides component data to the machine controls for selecting a suitable processing program. After half of the cycle time is over, the robot automatically turns the components on the rotary table to blast the other side. After the blast process is complete, the robot returns the finished work pieces to the pallet
Versatile rotary table blast machine with two turbines guarantees fast and efficient processing
The rotary table blast machine RDT 150 allows the blast cleaning of work pieces with different sizes and shapes. The table has a diameter of 1,500 mm and a load bearing capacity of 500 kg. To ensure the required short cycle times the machine is equipped with two Gamma 300G turbines, each with an installed power of 11 kW. Compared to conventional turbines, the Rösler Gamma turbines with their curved throwing blades in Y-design generate an up to 20% higher blast performance. At the same time they consume a lot less energy. The bulkheads mounted in front of the turbines also help reduce the cycle times and energy consumption. When the work pieces on the table are turned, the blast media flow is turned off, but the turbines continue running at full speed. This prevents costly energy peaks that occur when the turbines are decelerating and accelerating. Before the robot turns the work pieces, a special blow-off system removes residual blast media from the rotary table.
Optional manual loading increases operational flexibility
Around 90% of all components can be loaded and unloaded by the robot. If the component weight exceeds the capacity of the robot, such components can be loaded and unloaded by crane. Likewise very small components can be loaded in this fashion, when the automatic loading would require too much time. For safety reasons, in case of manual loading the turbines are completely turned off before the door to the blast chamber can be opened.
The sturdy design of the compact shot blast machine guarantees a high equipment uptime. For example, the blast chamber, made from tough manganese steel, is lined with easily replaceable wear plates made from highly wear resistant material. In addition, both sides of the Y-shaped throwing blades in the Gamma turbines can be used. This practically doubles their usable life. A quick exchange system allows replacing the throwing blades without having to dismount the turbines.
The highly automated Easy Shotblaster RDT 150 permits OTTOSTAHL the efficient blast cleaning of a broad range of sheet metal components with drastically reduced labor input and greatly improved working conditions for the employees.
About OTTOSTAHL
For over 80 years, the privately owned Rösler Oberflächentechnik GmbH has been actively engaged in the field of surface preparation and surface finishing. As global market leader, we offer a comprehensive portfolio of equipment, consumables and services around the mass finishing and shot blasting technologies for a wide spectrum of different industries. Our range of about 15,000 consumables, developed in our Customer Experience Centers and laboratories located all over the world, specifically serves our customers for resolving their individual finishing needs. Under the brand name AM Solutions, we offer numerous equipment solutions and services in the area of additive manufacturing/3D printing. Last-but-not-least, as our central training center the Rösler Academy offers practical, hands-on seminars to the subjects mass finishing, shot blasting and additive manufacturing. The Rösler group has a global network of 15 locations and approx. 150 sales agents.