The aerospace industry is in an era of profound innovation. Airplanes and air travel are transforming in response to the needs of the global economy, necessitating the building of aircraft at an accelerated pace.
With over 50 years of long-bed machining expertise, NWI is a contract manufacturer of complex structural components, sub-assemblies, and complete major assemblies of wing structures. The company supports leading OEMs producing commercial, business, and general aviation aircraft. NWI is now marketing its capabilities into military aerostructures, space launch vehicles, and ship building. The company is growing rapidly. Revenue was up 20% from 2021 to 2022, up 36% from 2022 to 2023, and up another 15% from 2023 to 2024, all on current contracted business.
Core competencies of this quiet powerhouse include precision machining of long and large aircraft components, forming of long and large parts, including autoclave age forming, large-scale processing, automated fastening of structural components, and integrated assembly of major aerospace structures.
NWI specializes in manufacturing some of the longest skins, stringers, and spars in the industry. State-of-the-art 5-axis machining technology allows the NWI team to produce large, monolithic, complex components. The company has made strategic investments in advanced long-bed machining equipment to meet the demands of rising production rates and high-quality surface finishes, adding 10 additional spindles since 2021.
“We are a focused factory for long and large aluminum machining for structural components upward of 100 feet long and 20 feet wide for the world’s leading aerospace companies,” says Brannon Pfeffer, NWI Senior Manufacturing Engineer. “Our niche in the market is long and large aluminum structures.”
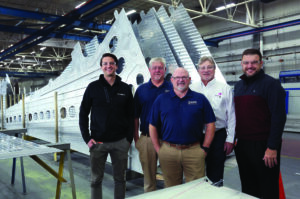
Trusted by top names in aerospace
NWI continually evolves, keeping up with advancements to best serve top-tier aerospace companies. “We’ve produced wing and empennage assemblies, and detail parts like skins, spars, and other components for the past 80 years. The precision, the surface finish, and the speed at which we produce them today is dramatically different than it was 20 years ago. That’s due to the cutters, equipment, programming, and the controls,” CNC Programming Manager Steve Freeman explains.
With the continued growth in air travel, NWI Aerostructures has been receiving increased orders for more parts as program rates increase. To capitalize on this opportunity, NWI saw a need to standardize its machining capabilities. After exploring purchasing new equipment, the NWI team determined that retrofitted Cincinnati gantry machines, complete with SINUMERIK ONE CNC controls from Siemens, were the best option to meet the growing and evolving demands of their customers.
“We looked at new equipment, but with the solid foundations of the machines we have a robust history of experience with, it’s a more-efficient and cost-effective process to refurbish them into great shape for the needs of today,” Pfeffer says. “We do the mechanical refurbishment work, adjust the alignment, and then add our tooling and chip collection systems. Our capital investment and lead time is about one-third of what new equipment would be. We have refurbished all of our equipment over the past 10 years.”
Economical Solutions from Fives Group
Fives Group is an international industrial engineering leader offering innovative solutions and products focused on boosting the performance of major industry leaders worldwide. Fives designs and supplies high-precision CNC machines, process equipment and production lines for various industries, including aerospace, automotive, and other complex manufacturing applications.
Through its Machine Tool Services and Solutions group, Fives offers complete life-cycle solutions for machine tools around the globe. This suite of services is aimed at maximizing performance — ensuring customers’ machines will continue to deliver to their full potential year after year. Supported products encompass the Fives family of brands, including the Cincinnati machines that are integral to the success of NWI.
As the original equipment manufacturer of the Cincinnati machines, Fives understands the fleet like no other company. It is a major benefit to have Fives servicing the equipment on a regular basis and a huge check in the pro column to have the OEM refurbish these machines.
To maximize investments made on precision-machining equipment, Fives brings more than 40 years of experience and expertise to upgrading and retrofitting existing machines with the latest controls, drives, motors, and spindles. SINUMERIK ONE from Siemens is integral to this process.
Retrofitting is the most cost-effective and sustainable full life-cycle solution Fives offers for its high-precision machines. The company believes in improving the productivity of in-use machines with retrofits resulting in nearly new machines capable of machining large aluminum parts with close tolerances.
Fives refurbished several machines at NWI, some with 30-plus years of successful service. Originally manufactured between 1985 and 1998, each machine has undergone a multi-stage refurbishing process. At the heart of each successful refresh, Fives relies on Siemens mastery of 5-axis CNC control.
Once installed, the new control package is commissioned and tested to ensure it delivers the operational performance levels desired. Fives also provides specialized training needed to ensure its customers get the most out of their new equipment.
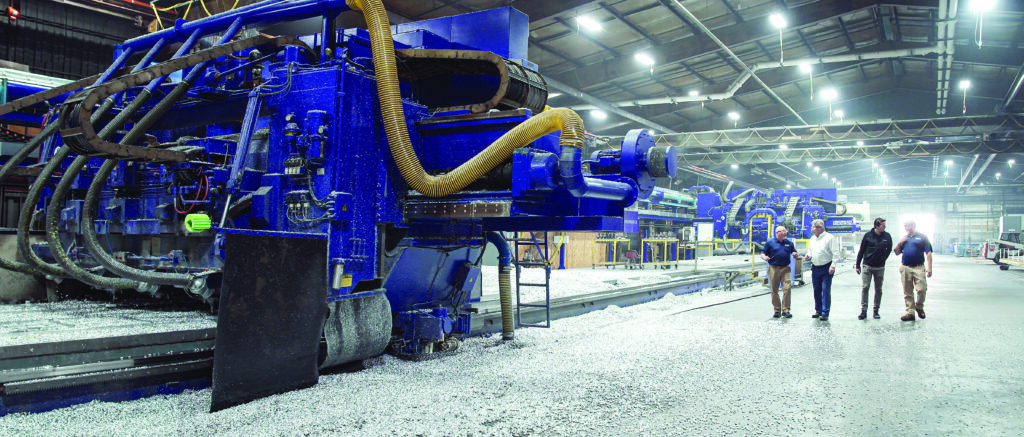
Game changing productivity increases
Switching to SINUMERIK ONE can result in a 30% increase in productivity for 5-axis machining. For 3-axis machines, you can achieve 20% faster results,” says Robert Stiefel, Head of Siemens Aerospace Vertical Market, U.S.
Gregory Mihalovich, technical sales manager at Fives Machining Systems, sums up the benefits.
“With the pioneering SINUMERIK ONE now powering its 10,000-rpm Cincinnati gantries, NWI will be even more efficient, helping the company increase its value to customers by focusing on innovation,” he says.
SINUMERIK ONE is based upon a multi-core architecture comprising state-of-the-art micro-processors, delivering faster CNC cycle times. By working in combination with our S7-1500 PLC, the SINUMERIK ONE control delivers the best productivity and security in the industry. “In the case of NWI, the biggest technology change is the CNC. You get the biggest bang for your buck by focusing on retrofitting the electronic components,” Stiefel says.
Stiefel also emphasizes the time-savings of a retrofit, which typically takes only 14 to 16 weeks (about 3-and- a-half months) and limits downtime. “A new machine purchase might take between six months and two years depending upon the size and complexity of the machine tool. It could be over two years between when you order the machine and when you machine your first part,” he says. “With a retrofit focused on a new control system, not only do you save money, but you also save time, and you benefit from measurable productivity improvements to help serve your customers better.”
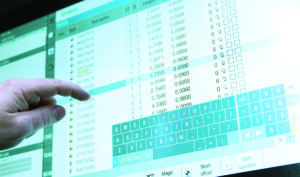
Stepping up to SINUMERIK ONE
NWI programmers and machine operators are finding the digital-native SINUMERIK ONE control a familiar tool for precision machining control. The functional characteristics of SINUMERIK ONE are similar to SINUMERIK 840D, but in terms of performance, the SINUMERIK ONE is light-years ahead, allowing the operator to achieve maximum machining speeds and improve the path precision for complex surfaces.
In addition to improving the first part yield and productivity of a machine, retrofitting improves the user experience, capitalizing on the synergy between the capabilities of the machines and the skills of the people, always a goal for Fives.
“Staying with Siemens CNCs has helped us be consistent,” says Jacob Benton, manufacturing engineer at NWI. “Both long-term employees and new hires have current experience running Siemens-equipped CNC machines. Every person who touches a Siemens SINUMERIK ONE is blown away by its processing speed, and our teams are quickly making the most of the increased functionality. Standardization across the factory is very important for NWI, with all of their CNC milling machines running a Siemens control. This decreases training requirements, improves flexibility, and standardizes maintenance and repair of parts.”
With its digital twin, the SINUMERIK ONE is a digital-native CNC and provides the basis for future-oriented production with machine tools. Capacity utilization is optimized, with tasks being consistently moved from the machine tool to the work preparation phase.
“Using the digital twin, you can run an actual program and get an exact example of how the program will run on the machine — even before making the first cut on the real machine,” says Robert Varney, Fives after-market engineering director. “In some cases, it’s troubleshooting before there’s trouble.”
Additionally, the advanced SINUMERIK ONE cybersecurity features, which are designed to meet coming requirements for government contracts, are ever more important to NWI and its customers.
The Fives approach to agile innovation, using still-viable equipment upgraded to the cutting-edge performance of SINUMERIK ONE, is a model for all companies looking to maximize production. Together, Fives Machining Systems and Siemens are moving aerospace manufacturing forward in ways that are economical, duplicatable, and sustainable.
For NWI Aerostructures, Siemens SINUMERIK ONE will ensure the company stays atop the “long and large” machining niche.