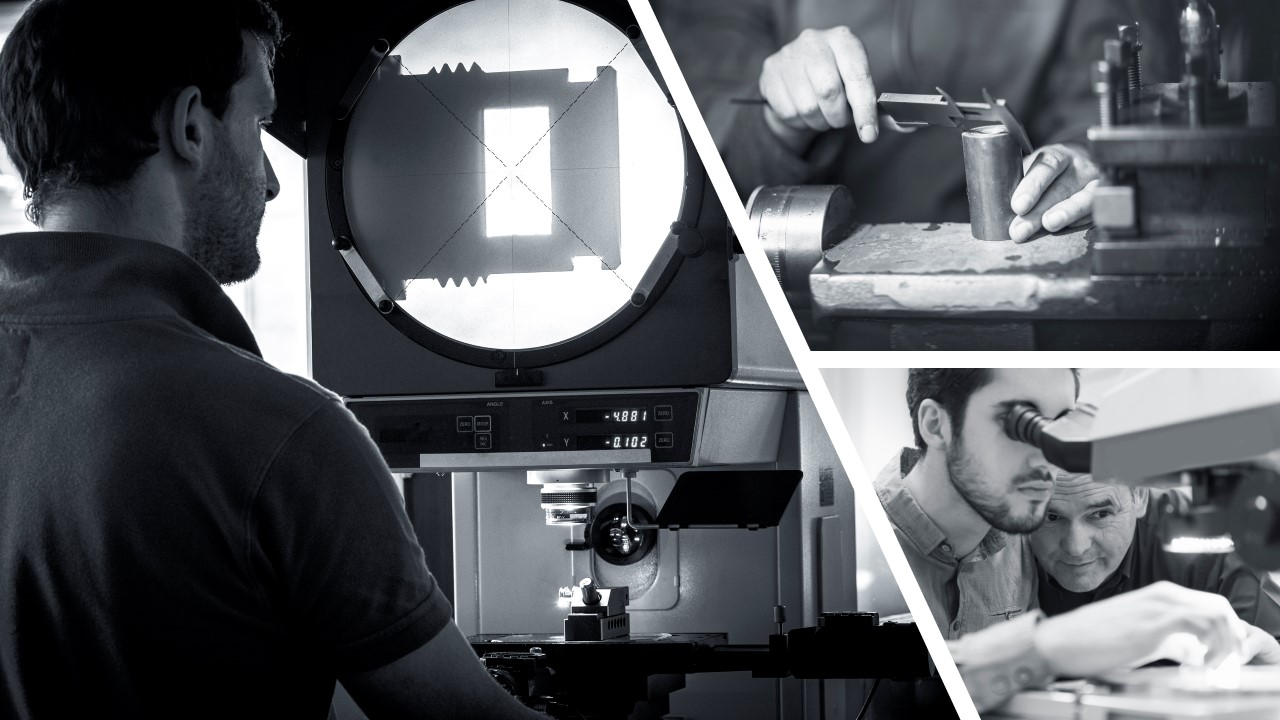
Metrology is the science of measurement. It encompasses the development, application, and study of measurement methods, devices, and systems. It establishes a common understanding of units, vital to human activity. Standardization is crucial for measurements to be meaningful. Metrology is a vast field, but can ultimately be distilled into three main concepts; scientific, legal, and applied or technical metrology.
Scientific metrology involves establishing internationally accepted units of measurement and the implementation of these standards into society. Legal metrology is the application of linking measurements back to reference standards, or traceability. Lastly, there’s applied or technical metrology which is concerned with the application of measurement, ensuring proper use of the measurement instruments, the calibration of the tools and quality control. These practices date as far back to almost 3000 BC, when the Egyptians established the cubit, based on the length of the Pharaoh’s forearm and hand, giving builders a reference for architectural developments including the building of the pyramids.
In the context of manufacturing, applied or technical metrology or measurement, refers to the numeric expression of a manufactured object’s dimensions based on a fixed reference (unit). These measurements are primarily used to ensure that parts and products are made to precise specifications and tolerances – which are generally focused on units of length. Precise measurements are crucial to ensure that products are of high quality, function as intended, and can be reliably reproduced.
Metrology in manufacturing typically involves using a wide range of measurement tools, such as micrometers, calipers, optical comparators, and coordinate measuring machines (CMMs). By using these tools, the dimensions and geometric properties of parts and products can be measured precisely. Measurements are used to confirm that parts and products conform to the intended design specifications, and that they meet the necessary quality standards. In many cases, clear traceability to component measurements are required to track batches or lots that are produced. Not only are increasingly large amounts of data capture and management necessary to track measurements for traceability – but shrinking part sizes and advanced material characteristics have also increased the complexity and frequency of these measurements during advanced manufacturing processes.
These challenges can be addressed by automating metrology steps within a manufacturing operation. One of the primary benefits of automated metrology is increased efficiency. Automated metrology systems can perform measurements much faster than manual methods (generally reducing work minutes to seconds of compute time) and can also collect and analyze data more accurately. This can help reduce the time to manufacture finished products and the overall cost of manufacturing, while also improving product quality.
We can categorize automated metrology benefits within a manufacturing operation into 7 key areas:
- Save Time: Automated metrology systems can significantly reduce time spent inspecting parts. Parts that could take 10-15 minutes to inspect and record data with manual tools can be done in less than a minute, allowing manufacturers to increase their profitability through increasing efficiency.
- Improve Accuracy and Consistency: Automated metrology systems can take highly precise and consistent measurements, reducing the likelihood of human error, especially reducing the repetition of the task which increases the chances of mistake. They help ensure the overall accuracy of the manufacturing processes and can help to confirm that parts and products are made to the same exacting standards every time.
- Reduce Labor Costs and Increased Flexibility: Automating metrology reduces the need for human operators to perform manual measurements, allowing them to focus on other areas helping to increase production. These tools require skilled metrologists to develop proper measurement programs and routines according to print requirements. However, once created, the system’s automation simplifies the procedures and allows a broader range of employee skill levels to help with QC tasks, addressing many of today’s challenges with skilled labor gaps.
- Reduce Scrap and Rework: With typical in-process checks, parts are inspected periodically. Due to these periodic checks, operators can be late to discover that parts are being manufactured incorrectly and either need to be reworked entirely or scrapped which can be costly with rising material costs. Automating metrology allows for earlier defect detection allowing manufacturers to save significant costs by addressing upstream processing and performance issues..
- Manage Data: Automated systems can collect and store large amounts of data, which can be used to identify patterns, track performance over time, and make data-driven analytics-based decisions. Data management supports transformation to Industry 4.0 digital connectedness..
- Improve Quality Control: Automated metrology systems can be integrated into various manufacturing control systems, allowing manufacturers to monitor and control the quality of the manufacturing process in real-time, and make adjustments as needed to improve the quality of the final product. Additionally analytics can be used with the trend data to identify and schedule preventive maintenance needs for critical machines. For example, your measurement system can help you identify a trend in steadily increasing measurements on parts produced on a mill, indicate this is wear on a cutting bit, and sending signals to operators or the machine tool to change it before a failure actually occurs and generates an unplanned downtime scenario.
- Enable Business Growth: Industries with strict part requirements like aerospace and medical typically need 100% part inspection, have tight tolerances going into the micron or millionths of an inch level, and call for specialized traceability, reports, and validation. Automated metrology systems provide the conditions for the manufacturing operations to be compliant with these requirements and enable sales into new markets and business development.
Overall, automating metrology in manufacturing can help to improve efficiency, reduce costs, improve product quality, and increase consistency. It can also provide valuable insights into the manufacturing process that can help to make it more efficient and effective. A tool that has helped manufacturers ranging from job shops to large aerospace and medical companies automate inspection processes has been Keyence’s IM-8000 Series Instant Measurement System.
Keyence’s IM-8000 Series uses a combination of an ultra-high-definition camera, telecentric lenses, and intelligent software to quickly identify a part (or multiple parts) in its field of view, extract part edges with optimal built-in lighting conditions, and accurately measure dimensions while automatically saving the data. The technology enables any operator to accurately measure up to 300 dimensions on a part in 3 seconds or less by simply placing the part on the system and pushing a button. The latest generation introduced an automated rotary that allows for 360-degree part inspection.
Using an automated optical comparator with an automated rotary allows for high-precision part inspection in seconds at the push of a button, in addition to automatically generated reports. Whether machined or turned parts, or injection molded parts, this tool was designed to address all of the key benefits of automated metrology.
About the Author
Manny Lopez is the Technical Marketing Manager – Quality and Metrology Systems – Keyence Corporation of America