Job shop owners know digitalization is coming. Now, they have a familiar and trusted machine tool partner to help them meet the challenge.
“There’s the closing scene in the first ‘Terminator’ movie,” says TRAK Machine Tools owner Steve Pinto. “Sarah Connor is escaping because she knows that Skynet is coming. She’s in Mexico, and a young boy points to the horizon speaking in Spanish that a storm is coming. And she looks off and she says, ‘I know.’”
Job shops are facing the digital adoption challenge across two fronts—toolroom and production. “The transition across the business will be difficult for job shops,” Pinto says. “Especially owners that do not have teams of engineers and IT specialists to help them evaluate and integrate new, digitally enabled machining operations.”
As a first step to help shops on the toolroom side, TRAK developed a line of machining centers, powered by the company’s popular ProtoTRAK® CNC. Now the company is introducing an all-new line of production-level machines empowered by the Siemens SINUMERIK ONE “digital twin” CNC platform.
The Transition to Digitalization
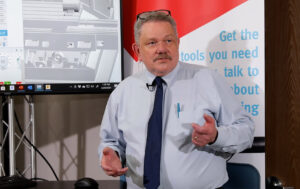
Tom Copeland is TRAK Chief Technology Officer. During his 40 years with the company, he has seen how job shops can fall behind during technology transitions.
“Most shops are still at step one, getting started with what I call the dashboard era,” Copeland explains. “They are basically connecting machines to software applications, then monitoring those machines from a managerial dashboard. The benefits of this first step are to sort out connectivity and security issues along with preparing the organization to make data driven decisions. But then shops need to take the next step. They need to implement software that connects machine tools and shop floor personnel. This provides the targeted information that enables an organization to implement new business models. Together with Siemens, we can help our customers take that next step.”
According to Copeland, Siemens is the right technology partner at the right time, and the reason can be summed up in one word: automation.
“Automation can mean any kind of mechanism that enables a process to go from part-to-part,” Copeland says. “The Siemens SINUMERIK ONE platform enables TRAK and our job shop customers to cross over into that level of automation. We do not need to build our own platforms with all of the related IT and software development. The Siemens platform is already there with their Control to MindSphere® connectivity and their support for common machine protocols like OPC-UA and MTConnect. Also, with the SINUMERIK ONE software development kit and their MindSphere API, TRAK is able to add new features that are targeted at specific markets without us having to write complex software from scratch.
Uplifting Toolrooms and Production
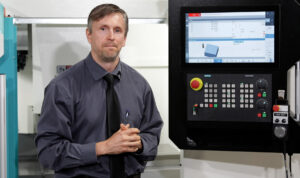
Leo Gammaitoni is TRAK Engineering Manager. He sees the company’s relationship with Siemens as perfectly aligned with TRAK in the delivery of digitally evolved production machines that are easy to adapt at the operator level.
“The Siemens control has long been the closest to what we’re doing in terms of conversational CNC, the ease of use, the ease of programming,” Gammaitoni says. “Our ProtoTRAK controls and machines serve prototyping and low-volume production. But machine shops also need that ease of use on production equipment, and Siemens was the No. 1 choice to partner with to do just that.”
Central to the digitalization strategy at TRAK is the adoption of the SINUMERIK ONE control’s “digital twin”. This software module, called Create MyVirtual Machine, enables machine motion to be visualized and exactly measured on a 3D plane. The digital twin workspace moves machine design, operation, maintenance, and operator training far beyond the limitations of current simulation software.
“Using Create MyVirtual Machine, I can see the entire machine in exact 3D before the machine is even built,” Gammaitoni says. “I can customize the machine, make changes, and see what happens. I can trace a tool path and be confident that it’s 100 percent accurate.”
Gammaitoni and TRAK plan to collaborate with Siemens to leverage the SINUMERIK ONE CNC platform to create other leaps forward in production-level machining. The integration of more powerful yet intuitive CNC opens the way to building production machines with much faster spindle speeds, improved surface finishes, faster setups, and parts completion. All of which contribute to faster time-to-market.
For example, by exploring within the SINUMERIK ONE CNC digital twin environment, Gammaitoni and his engineers proved that the motion of their new production machines could evolve from traditional linear ball guides to linear roller guides.
“We’ve gone to a more rigid production machine because we proved within the digital twin environment that we could take advantage of that greater rigidity,” Gammaitoni says. “This was also made possible by the Siemens control, which is capable of moving faster and cutting at higher speed rates.”
A New Set of Digital Tools
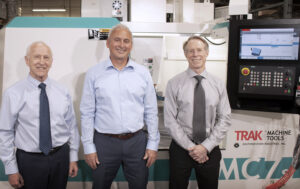
current owner Steve Pinto (right) see the Siemens SINUMERIK ONE control platform as the company’s way forward in the development of digitally enhanced production machines. Siemens account manager Chris Britton (middle) has been a collaborative partner in the journey.
Chris Britton feels privileged to have collaborated with the leadership team at TRAK Machine Tools for over 15 years. As the Siemens account manager, he has closely participated in the adoption of digital CNC technology at TRAK.
“It was never about selling features and functions,” Britton says. “When we talked about the SINUMERIK ONE platform and the path to digitalization, we didn’t say, here’s this incremental improvement in hardware with more features. We talked about a digitally enabled platform for job shop business evolution and the software tools to take you there.”
Within the Siemens digital twin design environment of SINUMERIK ONE, a numerically exact 3D tool path accounts for all related forces, including tool type and speed, part material, part shape, and machine rigidity.
Create MyVirtual Machine software enables the machine design engineer to see in 3D exactly how the machine will perform before actually building the machine.
Run MyVirtual Machine enables a job shop to use virtual 3D to dramatically cut part production time, train machine operators, and improve shop-wide processes.
ShopMill and ShopTurn software visually guide the simple and efficient setup of a production-level machine.
Owning the Challenge
Having found the right technology partner in Siemens, the company that pioneered the ProtoTRAK control for toolrooms everywhere is helping those customers confidently take the next step into digitally enabled production.
“Prototyping and production are different operations requiring different technology solutions,” Pinto says. “TRAK can now offer machine technology solutions across both sides of a customer’s business.”
True to its beginnings, TRAK leadership is seeing to it that the company continues to earn the trust of customers by helping machine shops survive and thrive. Whether you call it digitalization, IoT, or Industry 4.0, the way forward for TRAK starts with trust.
About Siemens Digital Industries (DI)
Siemens Digital Industries (DI) is an innovation leader in automation and digitalization. Closely collaborating with partners and customers, DI drives the digital transformation in the process and discrete industries. With its Digital Enterprise portfolio, DI provides companies of all sizes with an end-to-end set of products, solutions and services to integrate and digitalize the entire value chain. Optimized for the specific needs of each industry, DI’s unique portfolio supports customers to achieve greater productivity and flexibility. DI is constantly adding innovations to its portfolio to integrate cutting-edge future technologies. Siemens Digital Industries has its global headquarters in Nuremberg, Germany, and has around 75,000 employees internationally.
About Siemens Corporation
Siemens Corporation is a U.S. subsidiary of Siemens AG, a global powerhouse focusing on the areas of power generation and distribution, intelligent infrastructure for buildings and distributed energy systems, and automation and digitalization in the process and manufacturing industries. Through the separately managed company Siemens Mobility, a leading supplier of smart mobility solutions for rail and road transport, Siemens is shaping the world market for passenger and freight services. Due to its majority stakes in the publicly listed companies Siemens Healthineers AG and Siemens Gamesa Renewable Energy, Siemens is also a world-leading supplier of medical technology and digital healthcare services as well as environmentally friendly solutions for onshore and offshore wind power generation. For more than 160 years, the company has innovated and invented technologies to support American industry spanning manufacturing, energy, healthcare and infrastructure. In fiscal 2018, Siemens USA reported revenue of $23.7 billion, including $5.0 billion in exports, and employs approximately 50,000 people throughout all 50 states and Puerto Rico.
About TRAK Machine Tools
(Southwestern Industries, Inc.)
TRAK Machine Tools is well-known for its ProtoTRAK brand of CNCs and TRAK Machines. Founded in 1952 as a job shop serving the aerospace industry, it has been manufacturing ProtoTRAK CNCs since 1984 and selling them throughout North American and Europe. TRAK Machine Tools fields direct-to-customer Sales and Service Organizations throughout the United States in many of the areas that have high concentrations of manufacturing. Where it does not have its own field sales and service, TRAK Machine Tools serves customers via close relationships with independent distributors that share the core values of service to customers and community that has been the key to the enormous popularity of the ProtoTRAK and TRAK brands. The new initiative with SIEMENS will utilize the talents and reach of TRAK Machine Tools beyond the toolroom and into production and automation applications. For more information, please see www.trakmt.com.