At IMTS 2018, Siemens presented its popular Sinumerik CNC hardware and software solutions, offering dual tracks for the machine tool builder and end-user attendees from job shops and production departments of all types. Advancements in machine tool automation were demonstrated for various CNC machines — from basic milling and turning applications to multi-axis machining centers and the fully automated, flexible work cells used throughout the manufacturing industry. In addition, Siemens displayed its new Mindsphere “software as a service” concept, which enables machine tool users to gather, prioritize and access data in real-time, using edge technology.
Reflecting the company’s drive to the digital factory, a virtual experience for machine tool design and build functions was presented to the OEMs, while end-users experienced how the machines used on their shop-floors will be operated, managed, programmed and maintained in the future. In combination with the advanced motion control technologies and PLM services offered by Siemens, the full process chain from CAD to CAM to virtual simulation to production and performance assessment was on display.
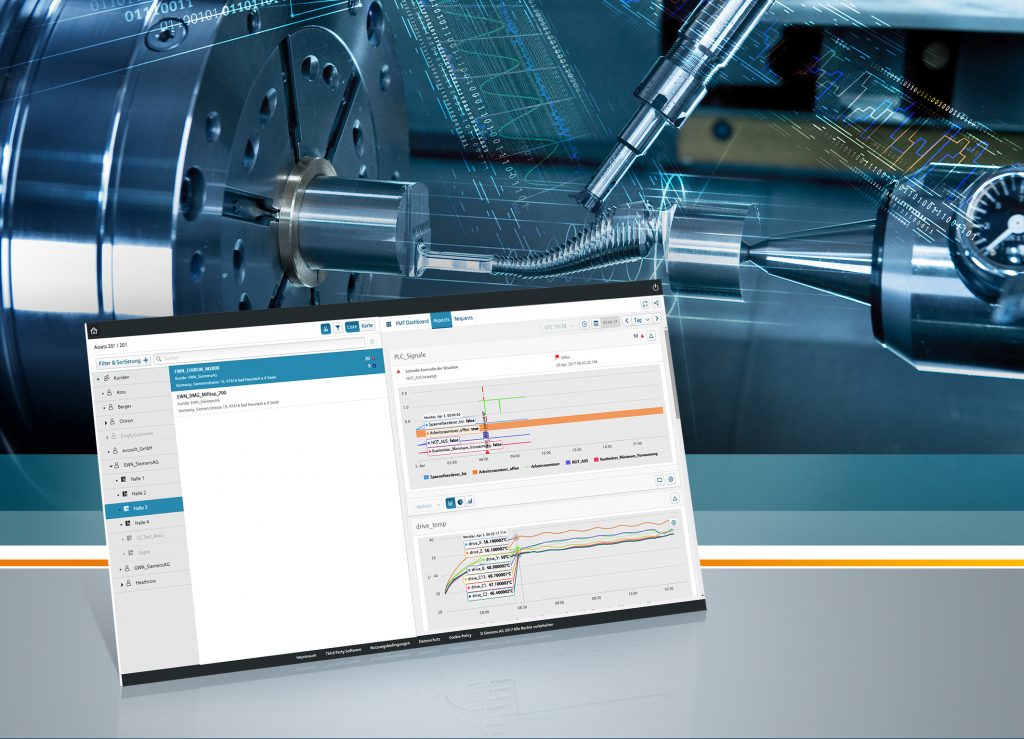
Siemens offers the machine tool builder an entire portfolio of CNCs, plus the integration of robotic machining and solutions for additive, in tandem with the advanced automation scenarios of today’s manufacturing environment.
Likewise, Siemens has taken a major step on the road to digitalization with Mindsphere, which offers machine tool builders and end-users alike a variety of customizable software and application options for the control and maintenance of their operations.
Enhanced Transparency at The Digital Enterprise
Siemens new Manage MyMachines, is one of the MindApps within the rapidly emerging Mindsphere concept. This cloud-based, “software as a service” enables the full data tracking of machine kinematics as well as production data and Manage MyMachines serves as the initial point of entry into this digital world, combined with edge technology.
Digitalization is no longer an intimidating notion for all types of companies in the manufacturing world. In fact, it is or soon will be an essential component in the operating philosophies at all companies. In response to this exciting evolution of Industry 4.0, Siemens opens the door to the digital world with Manage MyMachines, creating new and viable possibilities for increasing productivity, in combination with the highest achievable quality output and adherence to production schedules, plus reduced maintenance and service costs.
“Simply stated, this concept will be a gateway to the digital factory for all of our associates in the machine tool world, including builders, integrators and end users of all shapes and sizes,” says Sascha Fisher, head of the machine tool systems group at Siemens in the U.S.
For the builder, this development translates into an immediate ability to monitor the global install base. Shops and production departments, in tandem with their system integrators and other business partners, will benefit from a transparent display of all CNC equipment on the floor, regardless of location, brand, function or usage.
As a MindApp within the Mindsphere portfolio, Manage MyMachines is integrated in the cloud-based, open IoT operating system, as it allows access to all critical machine tool information, from bearing temperature to production by shift or job, all in a selectable priority scale, based upon user needs. Unexpected line downtimes and off-normal machine kinematic conditions can be quickly identified and rectified. Better yet, predictive maintenance can be programmed, so an upcoming failure can be anticipated, with alerts sent to a local distributor, for example, to deliver the needed components.
Complete asset management is further possible via Manage MyMachines, as resource consumption and energy usage are trackable, all in the cloud and all accessible through the app in real time.
The Next Level in CNC User Interface
This year at IMTS 2018, Siemens showcased its popular Sinumerik CNC Blackline touch panels with a new feature, the sidescreen enhancement. This development enables users to customize the panel of the CNC, laying out the operator panel in real time, using a drag-and-drop technology. Screens can be customized to view documents, camera projections, web server access information, access protection data for IT security protocols and even user administration.
Features and functionality such as the ongoing checking of the machine tool status, quicker and easier navigation, elimination of mechanical keys and adding new keyboards can be achieved with the sidescreen feature. The result is greater space savings with improved and highly flexible design and feature arrangement onscreen.
Sinumerik CNC sidescreen can be opened or closed on either the left or right side of the master operator panel and allows for positioning to suit the design and viewing angles on the machine for greater operator ease of use. The sidescreen works seamless with the Sinumerik Operate graphical user interface.
These Blackline Plus sidescreen operator panels are available in 16:9 aspect ratio, high-definition formats with multi-touch, scratch-resistant and non-reflecting panel technology, sealed for use in the harsh manufacturing environments yet sensitive enough to permit simple and secure operation while wearing gloves.
This feature is now offered on Sinumerik 840D sl models with 15”, 19”, 22” and 24” operator panels.
About Siemens
Siemens Corporation is a U.S. subsidiary of Siemens AG, a global powerhouse focusing on the areas of electrification, automation and digitalization. One of the world’s largest producers of energy-efficient, resource-saving technologies, Siemens is a leading supplier of systems for power generation and transmission as well as medical diagnosis. With approximately 372,000 employees in 190 countries, Siemens reported worldwide revenue of $92.0 billion in fiscal 2017. Siemens in the USA reported revenue of $23.3 billion, including $5.0 billion in exports, and employs approximately 50,000 people throughout all 50 states and Puerto Rico.