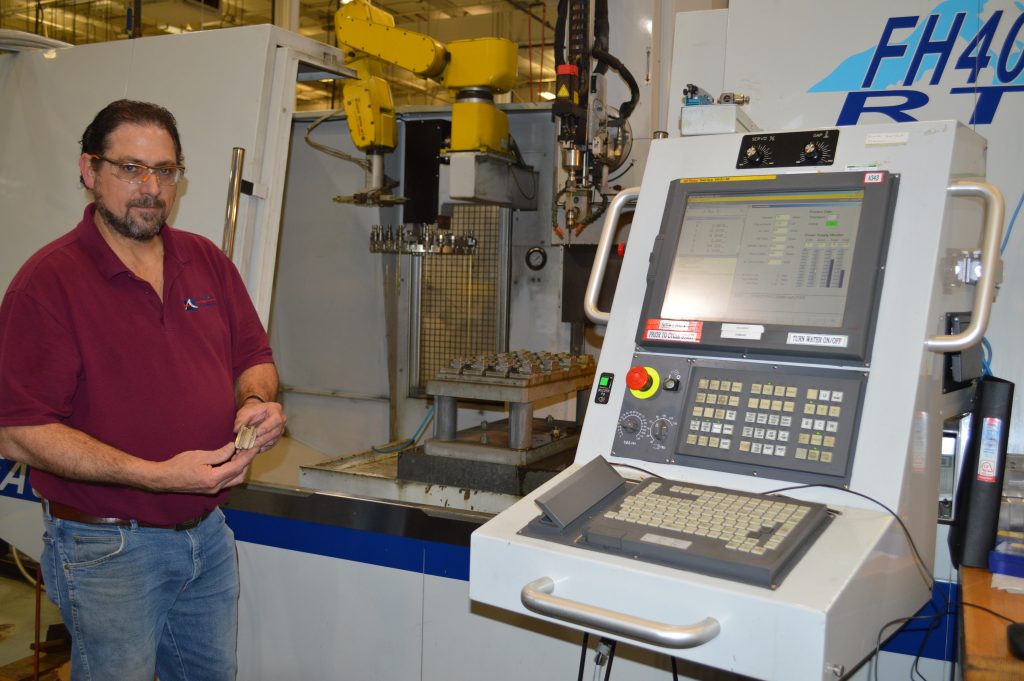
Aerospace Techniques (Middletown, Connecticut) has been delivering precision machined components for aerospace power generation and other uses since 1965. Today, the company manufactures a wide variety of unusual and complex shapes, working in myriad alloys and using state-of-the-art machining technologies, including fast hole electrical discharge machines (EDM). While aircraft components remain the focus of the company, Aerospace Techniques also produces parts for the industrial turbine, medical and electronics markets, owing to their reputation for high precision, superior quality control and innovative engineering teams.
The company’s core competence remains in blades and vanes for the hot section of aircraft engines. As these parts have evolved to the hollow configurations typically found on the market today, cooling holes became the norm for all the major engine manufacturers. Due to the high nickel and cobalt content of the alloys used, EDM and laser technologies have become the first choices for making the precision tolerance holes needed on such products.
At Aerospace Techniques, round cooling holes range from 0.010” to 0.190” diameters, creating the challenge of maintaining surface finish and low recast layers in the EDM processing. Additionally, because holes are often combinations of conical, round and shaped designs and in order to maintain reasonable production levels, it was necessary to find EDMs that would hold tolerance and provide a single point electrode to mill shaped hole geometries while producing the round hole through the airfoil wall, all in a single step.
Enter Beaumont Machine
Beaumont Machine has worked with Aerospace Techniques for a number of years, but was consulted for application assistance in this emerging area by the customer. A team led by General Manager Fady Elias and EDM Manager Bruce Morin reached out to Beaumont, for possible solutions. Beaumont has been a supplier to Aerospace Techniques, led by company founder and President Ed Beaumont.
As Fady Elias explains, “We entered the fast hole EDM arena in the late 1990’s and met up with Beaumont at that time. They’ve been supplying us machines since that time. In this case, we were seeking an ideal scenario of prep the program, load the parts, start the machine and run it in an unattended mode for 10 hours. I can say the team at Beaumont has helped us achieve that goal.”
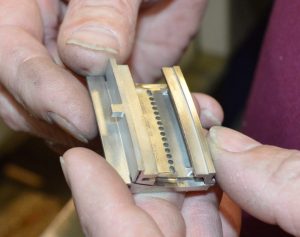
Bruce Morin seconds that thought. “I was a CNC programmer/machinist when I joined the company and really had no knowledge of the EDM world. However, due to the service and training we received from day one with Beaumont, I quickly became more familiar with both the technology and the abilities of the machines. With our Mastercam and Solidworks software plus the Fanuc CNC onboard the machine, we quickly discovered the best solution for the new types of work we were handling for our customers.”
Today, a number of Beaumont FH Series machines, equipped with robotic tool changers and tool carousels with six size guides and 18 electrodes, so all the diameter changes could be made automatically, machine the highly complex blades and airfoils produced at Aerospace Techniques. The machines work on a variety of nickel alloys, plus some stainless alloys, producing a wide range of hole patterns. A typical job might involve a 1-1/2” x 2” x ½” piece with 0.060” diameter flat bottom holes with 0.050”- 0.060” depths and .060 wide x .100 long flat bottom slots, requiring plunge milling plus secondary electrode handling and manipulation to create the contour shaping. A combination of ram and wire EDMs produces the parts with seamless transition. On one job, Morin notes the cycle time has reduced from one hour to 22 minutes and on one blade project, the production has gone from 15 pieces to 32 pieces per day. Aerospace Techniques processes workpieces up to 40” diameter, as well, requiring large work envelope machines. The total investment in 2017 has reached $2.7 million in new equipment, according to Elias.
But the best part of this scenario is that most of the operation at Aerospace Techniques occurs in an unattended work environment. Morin explains, “Following the training and initial runoff on the machines, which Beaumont delivered in a very thorough and step-by-step manner with my team, the operators quickly grasped the operation and moved into a lights-out environment. With only a 15-minute reload time on the workpiece carriage, they were up and running in a short time. The results have taken several forms. It frees up our time to do other tasks, such as tool room projects, as we manufacture our own part tooling, do TIG welding, dot peen marking and specialty cleaning approval protocols, per customer stipulations.”
In the Aerospace Techniques quality control center, likewise, a variety of procedures are done in-house, including CMM inspection, 3D optical comparator inspection, atomic absorption (AA) spectrum analysis, fluorescent penetrant inspection (FPI), computer integrated airflow testing and metallurgical micro-evaluation.
Beaumont Machine notes several other projects on which the company’s machines have proven successful, including a Joint Strike Fighter exhaust component where a $1 million savings has been realized.
Fady Elias, who emigrated from Egypt at 18 and now holds a Master’s degree in management with a focus on organizational behavior from Harvard University, brings an interesting perspective to this production scenario. “We knew the Beaumont machines were capital intensive, but their combination of service, performance and out-of-the-box thinking gave us numerous inspirations to guide the development of our work cell layouts and production scenarios. A particular challenge for us is the substantial amount of low-volume, high-precision work we do and Beaumont rolled up their sleeves and joined us in devising an optimum solution.” He further notes a collateral benefit of this development to his company in a market segment such as medical/orthopedic, where the similar challenge of low-volume, often one-off, work must be done with precision, while machining very tough materials.
BEAUMONT MACHINE
4001 Borman Drive
Batavia, OH 45103
Ed Beaumont – President
P: (513) 701-0421