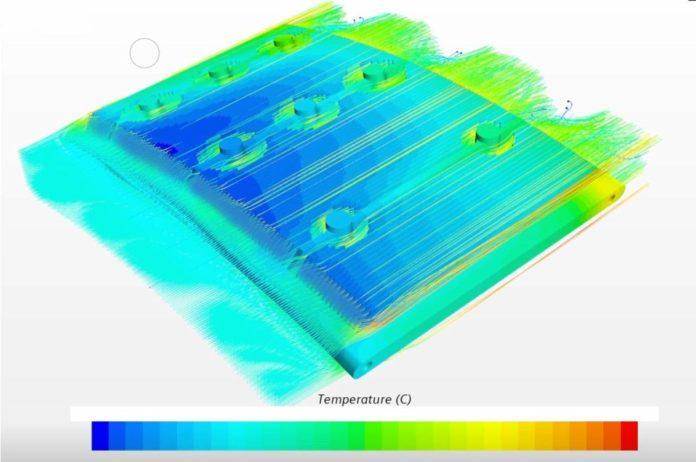
As consumer demand tapers off from the highs of the pandemic era, manufacturers and retailers alike are looking to shed excess inventory. Very few are looking to push the expansion button as they have in the past. It’s not always a function of available capital, often it’s reduced demand on the systems due to lack of customer confidence and lagging sales.
So, although it may be less than in the last few years, there is still capital in the budget—the question is what to do with it. The answer lies within the four walls of your existing distribution or fulfillment center.
With rising interest rates and a slowdown of e-commerce activity coming out of the pandemic, construction of new warehouses in the United States in 2023 is projected to decline 25% over the previous year, according to a recent report by research firm Interact Analysis. While new warehouse construction is expected to pick back up over the next two years, many companies may benefit more from updating their existing distribution or fulfillment centers than investing in greenfield projects.
Before the economy turns again, as it always does, now is the time for companies to prepare their logistics operations by implementing high impact, lower cost software and hardware upgrades. From increased individual KPI metrics and a lower cost per unit (CPU), you will be able to react quicker than your competition when the tide turns again.
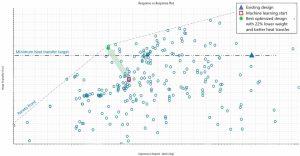
Software Upgrades
Software upgrades are usually troublesome. While companies want the increased performance or features promised, many struggle with creating the downtime for the upgrade. Oftentimes, they are unsure how best to proceed, and want the option of reverting to the old version if things don’t work out. Proper planning with the right team can give you the boost you need to tackle these projects. Using an outside consultant with years—if not decades—of experience performing and managing these types of cutovers can allay your fears and help ensure a seamless implementation.
If you’re operating a fulfillment center specifically processing thousands of orders every day for less than two units on average, it may be the opportune time to examine alternate strategies that rely less on physical labor and more on batching, grouping and cluster picking to improve efficiencies and reduce demand on human workers in your operations.
Typically, either your enterprise resource planning (ERP) or warehouse management system (WMS) controls the inventory, and whichever system controls the inventory should be the system for dropping orders, in any format, to the fulfillment center floor. Most ERP and WMS solutions have the capability to do many types of picking, and you should explore what you’re doing now to what you could be doing in the future.
Pick and pass (zone picking), batching, cluster picking and wave picking are all acceptable means of distributing orders to the floor based on your order profile(s). The critical piece is the ability of the floor associates to handle the pick methodology selected with the equipment at their disposal. Not having alignment on these software, hardware and operational processes will produce an unmitigated disaster for your floor leadership. Advance planning with visibility into all aspects of your logistics operations is required before you make any changes.
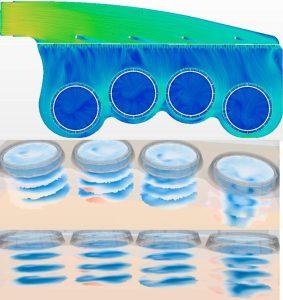
Hardware Upgrades
Hardware upgrades and replacements will breathe new life into an older system. While things may be working according to the design and use, there are some simple ways to extend life and increase the performance of older systems.
If you’re contemplating a dynamic switch to how you process orders as described above with software upgrades, there’s a very real possibility you will need to change some of your physical configuration. Before you see millions of dollars in upgrades, know that there are several areas that may require only moderate changes. If you’re changing from a retail environment to an e-commerce operation, one of those changes will be more significant.
In an e-commerce operation, you simply cannot keep up with even moderate demand in orders per day and lines per order without cluster or batch picking. Oftentimes, single orders are segregated and handled differently than multiple item orders. Cluster picking and combining them with dedicated packing stations utilizing automatic bagging operations can greatly streamline the process without a huge CapEx. Additionally, your revised OpEx will show a very quick ROI when balanced against labor costs and especially the availability of labor.
Using camera scanners instead of the typical ladder or picket fence style will not only accommodate a wider range of barcodes as customers change their requirements but should also provide a higher acceptance rate. This upgrade can significantly reduce labor costs associated with audit or jackpot lanes. With the right management oversight and hardware combination, audit lanes can become a thing of the past.
Another item that is typically overlooked is the outbound sorter. Considered to be one of the single most important functions in a distribution or fulfillment center, keeping it in top condition is usually left to the maintenance magicians to fix during stressful conditions, since we all know sorters only fail during times of high output demand. Taking the time and investing the capital to refit or upgrade your sorter during non-expansion phases of your company’s growth can go a long way.
If you’re using a belt, bombay or other low throughput style of sorter, now might be the time to invest in a shoe sorter. Shoe sorters offer the capability of sorting to both sides. Down lanes from the sorter are an inexpensive way to increase sort points, reducing the need to do so manually at the end of the existing down lanes.
Having a higher capacity per hour on the dock means fewer hours worked for the same output. Again, the goal is to reduce labor demand as hourly rates continue to escalate and will never reverse or go down. Changing the sorter may require an increase in the speeds from the conveyors that feed the sorter but that usually isn’t significant from a CapEx perspective.
And ultimately, if you have the CapEx, you should be exploring a goods-to-person (GTP) automation solution. There are almost as many options in this category as stars in the sky. Whether it’s an AutoStore, Geek+, stow, Exotec or other GTP solution, all of them can reduce labor demand, increase throughput and scale to your future state operations.
Most have a basic grid and numbers of captive totes/bins and robots to meet the current demand. One of the many attractive features is the ability to expand the system in the future without shutting down the existing operations. Adding to the grid, replenishment ports, picking ports and number of robots can all be accomplished during full-scale normal operations. It just takes educated planning and insight into what the overall model’s demands are.
All of these hardware and software options should be explored and vetted with your trusted supply chain engineer. Having the right partnership and team behind you to evaluate all options, develop the business case and aid you through the process can make all the difference between a great upgrade and a horrible, over-budget and untimely mess of an upgrade.
By David Latona, CEO, Tompkins Solutions
About the Author
David Latona is CEO of Tompkins Solutions. He can be reached at dlatona@tompkinsinc.com.