Have you ever noticed that one good idea often leads to another? In the world of motorsports, one idea sets off a cascade of events that has enabled over 330 combined wins in NASCAR, IMSA (International Motor Sports Association), and FIA (Federation Internationale De L’Automobile) Series. It also led to the creation of one of the industry’s top machine shops – Roush Yates Manufacturing Solutions.
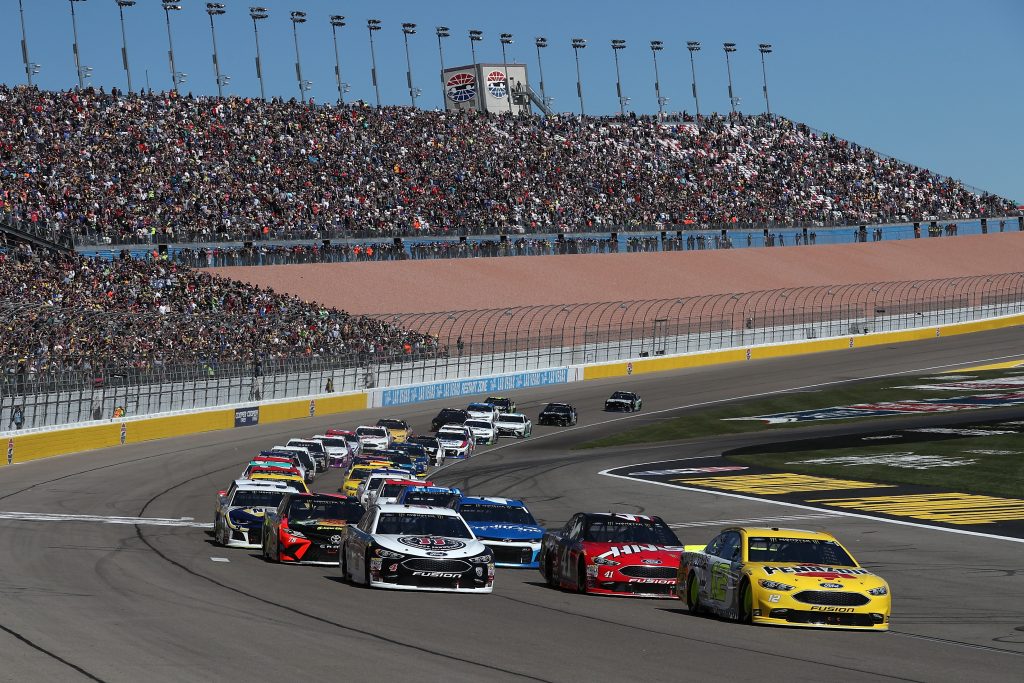
In the 1990s, Robert Yates of Robert Yates Racing discovered a way to gain an additional 50 horsepower from the Yates’ cylinder heads. With such a competitive advantage, NASCAR encouraged Yates to provide these cylinder heads to all Ford teams as well as share his template of success with NASCAR.
Faced with this challenge, a new production process needed to be developed so production could be scaled to meet this larger demand. At the beginning, it took more than three months to hand craft, blend, and refine the cylinder heads, each slightly unique from the other. To produce cylinder heads for all the Ford teams, Yates invested in his first piece of CNC equipment to compress the manufacturing cycle time and develop the repeatable processes that were required. Yates found CNC equipment provided a concise and accurate product and cut a three-month production cycle down to just three weeks.
In 2003, legendary engine builders Jack Roush and Robert Yates were the only teams building Ford engines in NASCAR’s premier series. To combine knowledge and technology, the men joined forces and formed what is known today as Roush Yates Engines. This team made a strategic move with Edsel Ford and Ford Motor Company and became the exclusive Ford Engine Builder for NASCAR, which was an innovative and adventurous endeavor for all parties in the modern era of racing. Led by President & CEO Doug Yates, they turned the partnership into a championship program and business. Today, Roush Yates Engines annually builds 1,000 engines that power 36 race teams in 6 countries across 3 continents.
As you may imagine, it takes a dedicated team of engineers, technicians, machinists and fabricators working together to build world-class race engines on a large scale. It also takes a lot of precision machining expertise. The high-profile nature of their business and extraordinary manufacturing prowess soon drew attention from manufacturers in other industries seeking to leverage Roush Yates Engines’ equipment, capacity and expertise. Roush Yates Engines leveraged their experience and culture of winning to form Roush Yates Manufacturing Solutions (RYMS), a fully integrated CNC and manufacturing facility located in Mooresville, North Carolina.
RYMS has evolved into a 30,000 square foot facility with more than 40 premier pieces of CNC equipment. Capabilities include CNC 5-axis milling, Mill-Turn, CNC turning, Swiss turning, and EDM. These capabilities enable RYMS to manufacture a wide array of components from various materials including aluminum, brass, titanium, CRES, high temperature alloys, and plastics.
Annually, RYMS produces over 150,000 machined parts for the racing, aerospace, defense and automotive industries – and they’re growing. With expertise in multi-axis machining of complex geometries and quick lead times, RYMS is well-qualified to supply parts to any industry where speed and precision are a prerequisite.
RYMS leverages relationships with industry leaders like Nikon, L.S. Starrett, Mitsubishi Materials USA, Mitee-Bite, Mastercam, Safety-Kleen, and TYKMA ELECTROX. These relationships provide unique benefits to the manufacturing process and RYMS benefits from collaboration with other experts in the field.
Growth and customer satisfaction are fueled by RYMS’ endless pursuit of quality and zero-defect manufacturing. To ensure quality, RYMS has developed a world-class quality lab to provide part inspection and documentation to meet and exceed customer expectations. They use advanced technologies and the latest equipment from premier partners like Nikon and L.S. Starrett to meet the rigorous ISO 9100 / AS9100 Rev D standards.
The internationally recognized AS9100 Rev D Quality Management System standard enlarges the requirements of ISO 9001 to meet the demands of the automotive, aerospace, and defense industries. This standard is strongly supported by the aerospace industry as its principal certification. RYMS is also ITAR compliant and DLA registered.
RYMS is in growth mode. To raise their industry profile and reach a broad buyer market, RYMS turned to SourceHorizon MFG. SourceHorizon is a sales and marketing firm that specializes in the manufacturing sector. The company has developed an Advanced Manufacturing Supplier Network that consists of world-class suppliers of CNC machining, metal fabrication, design-and-build, and build-to-print services. Member companies are promoted online and through highly targeted sales campaigns. Through SourceHorizon and the Advanced Manufacturing Supplier Network, RYMS has gained access to motivated buyers and Request for Quote opportunities that matches RYMS’ strengths and goals.
Bob Ucman, VP of Manufacturing for RYMS had this to say about the SourceHorizon relationship.
“We are known for delivering premium parts to our customers where failure is not an option. Our manufacturing facility leverages some of the best manufacturing engineering experts in the industry and our advanced manufacturing capabilities are top-of-the-line. Our desire at RYMS is to expand our services to a broadened industry network. The expert team at SourceHorizon can assist us in this endeavor. The proof is in their results and we look forward to working with them.”
“We’re honored to work with and promote Roush Yates Manufacturing Solutions,” said Perry Gathings, SourceHorizon’s Director of Business Development. “Roush Yates is an industry leader with a terrific vision for the future. What’s more, they have the equipment, capacity, and expertise that manufacturing buyers want. I’m confident SourceHorizon can help them reach, engage and convert those buyers into long-term, mutually beneficial relationships. We’re looking forward to helping Roush Yates turn their vision into reality.”
The business magazine “Forbes” notes that, when customers recognize a company as an authority, that company becomes the go-to organization for the area of expertise. There is no doubt that much like Roush Yates Engines is known as a leader in motorsports engines, RYMS will continue the legacy of innovation and become a go-to organization for machining and contract manufacturing.
About SourceHorizon
SourceHorizon connects buyers with suppliers that have the right equipment, capacity, and expertise for their projects. With multiple, well-qualified sources for CNC machining, metal fabrication, design-and-build and build-to-print services, SourceHorizon can help you find the right supplier for your project.