OVER THE RECENT YEARS, THE EVOLUTION OF SUCH CONCEPTS AS CONDITION MONITORING AND ADAPTIVE CONTROL HAVE BEEN SUBSTANTIAL.
Condition monitoring, as the name implies, watched the relationship between theoretical and actual speeds and feeds, making preprogrammed or set adjustments, as needed. Adaptive control was the next iteration, as the CNC could detect subtle differences in tool and workpiece conditions and adjust the cutting “on the fly” as the cycle proceeded.
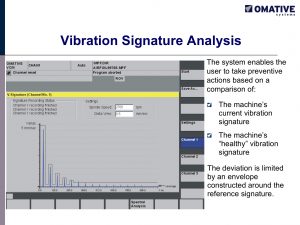
In the advanced world of highly complex, non-linear shapes found in the aerospace and especially the medical/ortho markets, the transformation orientation concept took the computation of the cutting path to a whole new level, basing it on the tool tip relationship to the workpiece, combined with a look-ahead function. Additional sensing hardware and probes were required and are still, today.
However, a recent development has come over the horizon that is based purely on software. This software is loaded into the CNC, provides custom screens to the programmer, operator and maintenance personnel. It monitors all spindle digital signals and literally “learns” the cutting condition, adapting the motor, drive, feed and spindle speed accordingly to compensate for a variety of conditions, including workpiece material variances, distance to workpiece, cutting tool wear and more.
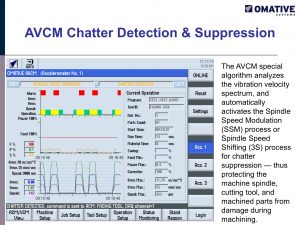
While additional sensors are still required to monitor vibration and tension, most other conditions are detected by the software, in process as the first parts are cut. The software adapts to any cutting machine, regardless of axes involved.
Geared for Production
As a result, this new software development is geared more for the production department, but also for the mid-sized job shop or contract manufacturer producing a few hundred pieces. With the cost of software today, plus the fact this add-on can be done on a single machine up to a full work cell or production line with dozens of “identical” machines involved. In that latter case, each machine learns on its own and makes adjustments in process, with all data available to the upstream control operation.
In practical terms, the software can drive cycle time reductions, prevent tool overload and breakage, extend tool life and protect the tool, spindle and machine, all the while furnishing real-time reporting.
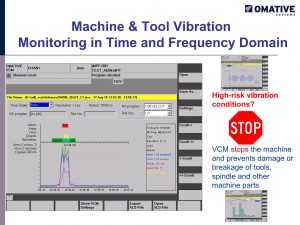
The software allows full motion programming, automatically compensates feed and spindle speed, plus it provides all the background data screens in real time for instant monitoring or adjustments. As a result, with the ongoing movement toward digitalization in the shops and factories of today’s competitive environment, such software can enable stats to be extracted from machines worldwide for a multi-national manufacturer or a machine tool builder looking to do comparative analysis on its install base.
In addition, the emergence of the cloud as a viable business platform today enables the CNC builder to interact with the machine builder and end user communities in ways never imagined, just a decade ago. This new software, for example, can be monitored by the CNC provider to track real-time spindle conditions in tandem with the machine builder for design improvement possibilities, as well as the end user for OEE data gathering.
The proper care and “feeding” of your spindles can help keep your machines happy companions to your production process. For more information on this latest development in CNC, give me a call.
About Siemens USA
Siemens Corporation is a U.S. subsidiary of Siemens AG, a global powerhouse focusing on the areas of electrification, automation and digitalization. One of the world’s largest producers of energy-efficient, resource-saving technologies, Siemens is a leading supplier of systems for power generation and transmission as well as medical diagnosis. With approximately 348,000 employees in more than 190 countries, Siemens reported worldwide revenue of $86.2 billion in fiscal 2015. Siemens in the USA reported revenue of $22.4 billion, including $5.5 billion in exports, and employs approximately 50,000 people throughout all 50 states and Puerto Rico.
About Randy Pearson
Randy Pearson, a long-time veteran of the machine tool industry, is a Siemens International Business Development Manager. His special interests include the many levels of training on CNC machine tools, which he conducts through the various seminars, workshops and classes the company conducts with machine tool builders and dealers, at vocational/technical schools and onsite at shops, as well as at the Siemens training facilities around the country. If you have questions or comments on this article or CNC in general, Randy can be reached at (800) 879-8079 or (847) 640-1595. His e-mail is randy.pearson@siemens.com.