In the 1870s, the Wizard of Menlo Park, a nickname by which Thomas Edison was widely known, worked with his father to create a research and development facility located in Menlo Park, New Jersey. The facility would soon be home to many important inventions of the time. These included the phonograph, on which Edison reportedly recorded the phrase “Mary had a little lamb,” and in 1878 the lightbulb which then was utilizing a bamboo filament that allowed for 40 hrs of continuous electrical driven incandescent light. Thomas Alva Edison went on to create the first power grid in 1882. In 1892, financier JP Morgan arranged for a merger between Edison’s Edison Electric Company and Thomson-Huston Electric Company which created the eventual global conglomerate General Electric, or GE.
From that day, innovation has been deeply rooted, encouraged, and applied in everything from advanced jet engines to materials science and digital transformation, from healthcare to power solutions and predictive analytics at GE.
According to GE’s website, from the creation of Edison’s power grid in 1882, “GE has played an integral role in generating power and delivering it to users all over the world. We continue to blaze trails in everything from gas turbines to transmission utilities.”
The former power businesses of General Electric will be spun off in the first half of 2024 as GE Vernova. From this point forward in the article, we will refer to GE Power businesses as GE Vernova
Jay Bryant is part of the GE Vernova’s Gas Power business line, which is the OEM of several Heavy Duty Gas Turbines (HDGT’s). Specifically, Bryant is the Product Line Manager of one of GEV’s gas turbines known as the 7E.03 gas turbine. He describes this product line as a very reliable, industrial, and rugged GT [gas turbine] with a lot of flexibility. “While it definitely isn’t the biggest or even the most efficient GE gas turbine, it is the most reliable and flexible,” says Bryant.
I’ve known Jay for almost 50 years – when he makes a categorical comment about reliability, I can tell you it comes from a place of deep understanding of not only the operating mechanics of the turbine, but also how the gas turbine is being used in the field as well as its historical performance. “Think of the 7E.03 as the equivalent of the F-150 in the Ford portfolio,” he says, without knowing that he just gave me the perfect frame of reference. As an owner of an F-150, that brought it all home and immediately I understood what he meant about reliability (I love my truck!). The 7E.03 has a fast-start cycle that can deliver 100% of its maximum load in 10 minutes, it operates at 60 Hz, it can accommodate a full range of fuel alternatives, all the while delivering a simple cycle output of 90 megawatts of power. To put that in perspective, 90 MW is enough to power nearly 65,000 average US homes, based on metrics used by GE.
Incorporating Additive Manufacturing
Of course learning more about the advanced manufacturing used in this gas turbine would probably take significantly more space than we have for this article, so we narrowed our focus to additive manufacturing. Before we dove into questions about applied additive manufacturing in his product line though, Jay said we needed to understand a bit about the moving parts and the stationary parts of the gas turbine and how the unit works. Operationally, the initial system to understand is the Compressor section. This is where air is compressed into the unit much like a jet engine. This “squeezed” air is then mixed with some type of fuel source which is usually natural gas. The flammable mixture is ignited in the Combustion section, where the natural reaction to the ignition is the expansion of hot gases. These hot gases are guided through the Turbine, where blades rotating from the forces of the expanding gases cause a shaft to turn which drives a generator.
Blades on both the compressor rotor and turbine rotor shafts are rotating parts and the forces to which they are subjected from the expansion gases are very high. Combustion hardware and airfoils attached to the casings are called stationary parts. “To date most of the parts [that are using additive manufacturing] have been combustion components or stationary components in the Turbine rotor section of the gas turbine,” says Bryant. “With combustion hardware, emissions (CO, NOX) can be greatly impacted by the internal geometry of the fuel nozzles which drives the mixing of the air and fuel. Additive manufacturing allows GEV to print parts with better emissions performance that would be extremely difficult and more expensive to cast with traditional processes.”
“Another successful area of additive manufacturing application has been with stationary components in the turbine section. Typically, the turbine section operates at temperatures at or beyond the melting temperature of the metal. However, by using internal cooling techniques or the application of thermal barrier coatings (TBC) on the surface of the part, we can manage that temperature impact. Similar to the complex internal fuel passages in fuel nozzles, additive manufacturing allows for more efficient internal cooling passages in stationary components that require less cooling air to be pulled from the compressor. Instead of using the air you’ve worked so hard to compress for cooling, that air can remain in the turbine flow generating more work in the turbine section. This leads to increased output (Megawatts!) and better efficiency (aka less fuel required). Same story again, additive manufacturing allows you to build creative designs that you just couldn’t manufacture with traditional casting processes.”
Crossing the Additive Manufacturing Chasm
So when did one of the most historically innovative companies make the commitment to Additive Manufacturing? It definitely wasn’t yesterday or last week. “GE went all in on Additive Manufacturing in 2016 with the acquisition of Arcam AB and Concept Laser GmbH, which when coupled with GE Gas Power’s Advanced Manufacturing Works center in Greenville, SC, allowed the engineering team to truly explore the full potential of additive manufacturing. For combustion components, like fuel nozzles and emissions controls, GEV was able to leverage our full scale combustion lab in Greenville to demonstrate the performance and capability of the additive manufactured combustion hardware. This gave us confidence to try parts in customers units which delivered significant improvement in emissions and thermal performance levels.”
In a video available on YouTube, entitled “The Power of 3D Additive Printing – In the Wild – GE,” Adam Savage tours the Additive Manufacturing facility in Greenville that makes 3D parts for the gas turbines. The video chronicles the design and additive build of a stationary part, a shroud, for an HA gas turbine. It is immediately evident that this isn’t a science project or a proof of concept, but rather a dedicated Additive environment – there are multiple metal additive 3D printers, which use Cobalt and Nickel-based alloys, and in which each plays its own contributing role to the overall capacity, as evidenced by their X-Men™ names such as Storm, Wolverine, Mystique, Juggernaut, Cyclops and Havoc. A key point made in the short video is that an additive manufacturing advantage is that those drawings you’ve been making on your Starbucks napkins or other napkins to keep track of free flowing group ideas or individual moments of ingenuity from pop up collaborations – well, they can be built now. The complex geometries are no longer the main design challenge. Free flow of information at higher frequency is the result. Designing for additive manufacturing is the term you will hear now. In the video it looks like the machines utilize powder bed fusion techniques with selective laser sintering, techniques discussed in our August 2023 edition of Industrial Machinery Digest.
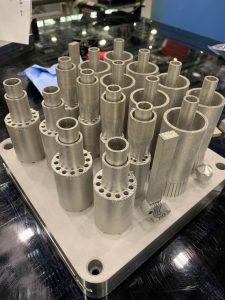
Looking Over the Horizon
We asked Bryant to give us some perspective on the tradeoffs for additive manufacturing in his product line. “As you can see in the attached picture of a printed tray with several different fuel nozzle tip designs, additive really accelerates the ability to create prototype concept parts in an inexpensive and timely manner. That tray had a print time of ~40 hours. There is some post printing machining and heat treatment before lab testing but we can go from design concept on a computer to physical lab testing in 4-6 weeks whereas the same part may take 6-12 months with traditional casting and post-cast machining, assuming you could even physically achieve the internal passages.”
“We are now using additive manufacturing to develop a new combustion system capable of burning 100% hydrogen without the need for a NOX diluent (aka dry combustion). In 6 months, we have designed and printed ~40 subscale concepts and are now in the process of testing them. We will down-select the best 1-2 performers for a full scale test. Without additive manufacturing, we would have been limited to 4-5 concepts taking 2-3 times longer and spending significantly more in development costs. Additive provides significant benefits in product development.
For production hardware, the speed of printing versus casting is a significant advantage for certain parts. The speed and relative ease of printing different designs is a material benefit to the supply chain management process. Inventory levels and customer service levels can be improved. From a customer service perspective, we have some gas turbine models that are 50+ years old and we no longer stock all the replacement parts for these units. Additive manufacturing offers a realistic ‘print to order’ capability to support these older models and keep them operational for the owner.”
In recent editions we have talked about the linkage between digital transformation and additive manufacturing. How does Bryant see the evolution of additive manufacturing as digitalization grows its product lifecycle footprint? “Additive manufacturing will continue to evolve and offer increased benefits as designers and engineers become more understanding of its vast capability. We still have instances where designers unintentionally trap themselves in the mindset of what can be built with traditional manufacturing processes as opposed to what can now be printed. So that is a people learning curve that we have to manage.”
“Additionally, the powders used in additive manufacturing will continue to get more capable, expanding the areas where printed parts can be used. One final interesting area of development is the concept of printing the casting mold itself with very intricate internal passages and then using a traditional poured casting process. This offers a similar cycle time to go from a part design on a computer to a casted part as is currently possible with additive manufacturing. Additive manufacturing will continue to push the boundaries of weight, strength, and heat capability leading to continued improvements in the gas turbine industry. Advancements such as decarbonization via hydrogen fuel and improved efficiency will be critical contributions to the energy transition currently underway.”
A Primary Focus
GE now lists Additive Manufacturing as one of its business focus areas, along with Aerospace, Capital, Digital, Power, Renewable Energy, Research, and Licensing. GE’s website positions the Additive Manufacturing business as a partner that can provide experience, consultancy, machines, software, and even powders for additive manufacturing. The technologies highlighted in the Additive business include Direct Metal Laser Melting, Electron Beam Melting, and Binder Jet metal additive. GE Additive’s AddWorks™ comprises 70+ global engineers that are singularly focused on operationalizing additive manufacturing within their client’s manufacturing environment. This allows customers to accelerate innovation, reduce risk, lower costs, and improve part performance and processes. Offerings include workforce enablement through Consulting Services or formal Training, various Qualifications, as well as speed to low-rate initial production through Engineering Services in which customer input is used to look at everything from material qualification, to design for additive manufacturing, to validation of designs and manufacturing processes – with engineering work being initiated and driven from just a set of requirements as input.
GE Vernova is committed to Additive Manufacturing, and GE is committed to Additive Manufacturing. Shouldn’t you? Send me an email to trey@indmacdig.com and let me know your thoughts.
Please see www.ge.com/additive for more details and information on GE’s Additive business.
Additive in Action
An example of a creative design that is completely aligned with Bryant’s comment regarding the advantages of additive manufacturing, is a 3D-printed advanced secondary fuel nozzle (ASFN) tip which was designed and manufactured by GE as the newest upgrade for their 7E turbine. Cooperative Energy, in Moselle, Mississippi needed a fix for its 107EA gas turbine, as it was getting uncomfortably close to breaking emissions rules. GE’s ASFN provided a path to meet the reduction, allowing Cooperative Energy to move away from an underfiring situation which had been put in place to meet CO2 output regulations to a lower NOx, to a higher megawattage situation – with an ASFN installation of less than 48 hours, and a new ability to overfire in a compliant manner. The end result was significant improvements which are not available with traditional casting.