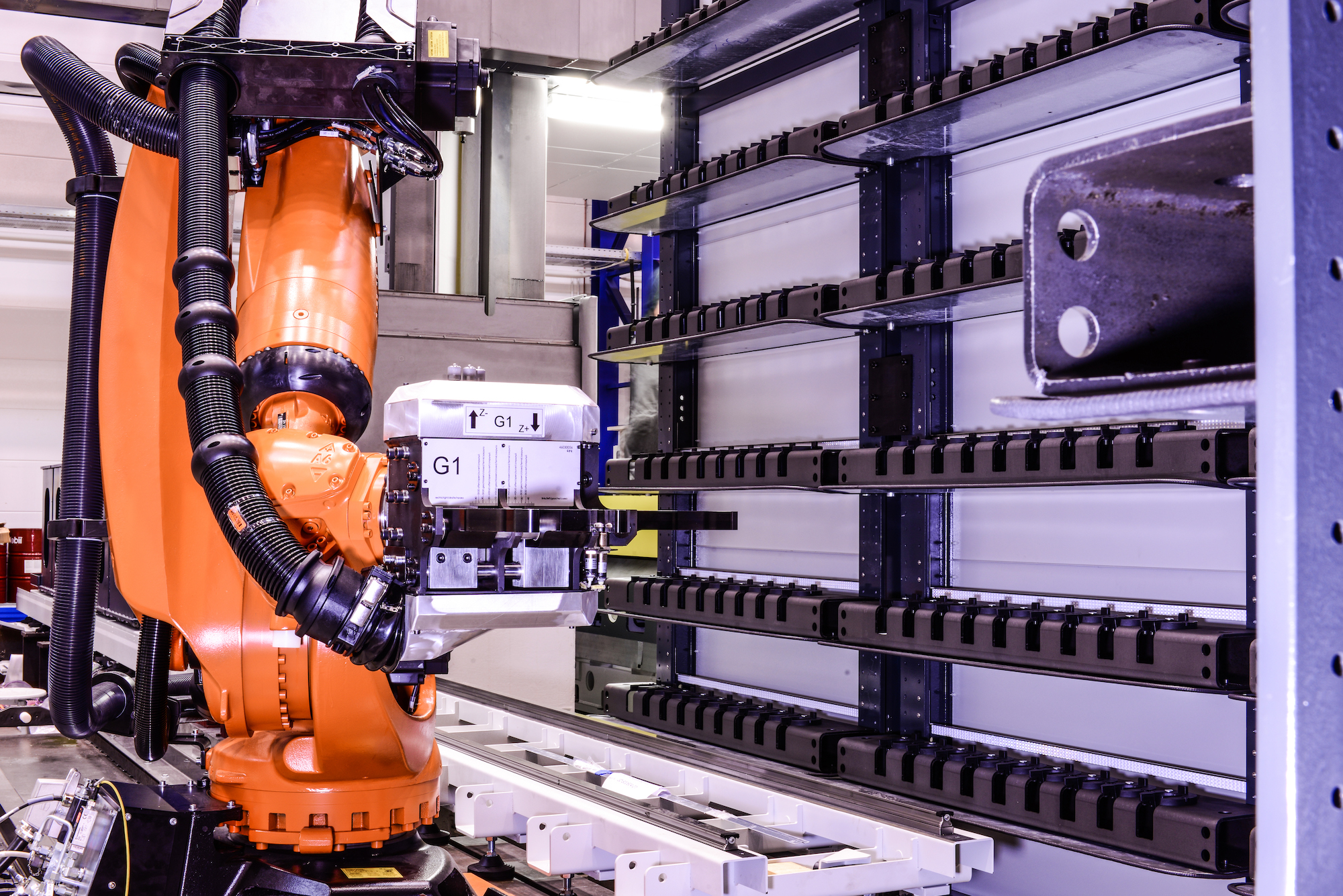
In a significant investment for the future, Metalex Manufacturing located in Cincinnati, Ohio selected Starrag to supply a large-capacity, multi-axis Droop+Rein portal-type machining center for their new Center for Advanced Large Manufacturing.
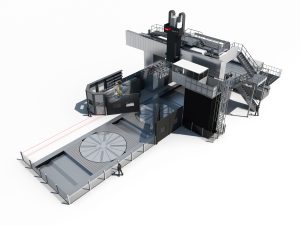
The machine – the largest ever installed by the Cincinnati-based contract manufacturer – will provide it with the ultimate in flexible production capacity to meet all Metalex’s foreseeable demands in terms of producing highly-accurate milled and turned workpieces in a single set-up.
The six-axis Droop+Rein T series machine is projected to not only satisfy existing projects but its extraordinary machining envelope of up to 709 inch table length, 374 inch between the columns and 276 inch under the spindle will certainly also attract new work – thus further ensuring Metalex’s success in the market of high quality manufacturing.
The portal type milling and turning machine – which is being specifically configured to meet Metalex’s current and future needs – offers an expansive 748 inch in X- and 354 inch in Y-axis. The 276 inch vertical clearance is covered by the 118 inch of ram stroke (Z-axis) and a continuously moveable crossrail of 217 inch (W-axis). The C-axis integrated in the ram with infinite rotation and the +/- 203 degrees Fahrenheit swiveling B-axis of the universal fork-type milling head complete the 6-axis.
The impressive 136 hp main spindle transfers up to 66,372 lbf in to the heavy vertical and horizontal milling head. A heavy duty fork-type head and a spindle cartridge change fork-type head both enable 5-axis operation and a slim spindle extension rounds up the initial milling head configuration. All heads will be designed, built and tested by Droop+Rein in Germany. Furthermore, the machine will be prepared for more heads to be fitted in the future as new jobs arrive. The versatile 400 pockets robot tool magazine ensures automatic loading of three different tooling systems into the selected milling and turning heads.
A distinctive feature is the table design. The X-bed carries two 236 x 315 inch tables that can be operated separately under the spindle while the other one is unloaded outside the machining area. Coupled ‘in tandem’, the tables can be extended to an enormous length of 709 inch for machining extra-long workpieces. In addition, each table holds an integrated 236 inch rotary table that utilizes the 2 x 149 hp main drives to turn components of up to 440,925 lb weight (using one of the turning tool holders provided in addition to the milling heads) or to position as a C-axis for high accuracy milling and drilling operations.
The result will be the ultimate one-stop precision machining source for extra-large components with complex geometry that require precision tolerances.
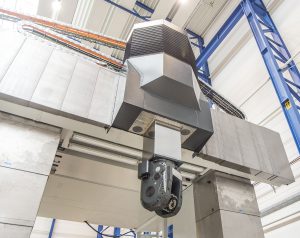
Established in 1971, Metalex is a performance-driven contract manufacturing company, specializing in producing high-quality complex workpieces for a wide range of market leaders in the Aerospace, Energy, Marine and Consumer Goods industries.
Metalex’s desire to source a machine that would not only satisfy current production needs but also meet all projected demands in the years ahead saw it contact a number of machine builders, including Starrag, which in the past has supplied it with a number of machines (a Dörries vertical turning lathe and two Starrag STC horizontal five-axis machining centers).
According to Droop+Rein Product Sales Manager, Heiko Quack, “We sat down with Metalex to discuss what was needed – in short: a very flexible, large-capacity and high-accuracy machine with 5-axis capability that would efficiently accommodate a variety of parts in a range of materials and produced to tight tolerances.”
“Applying our proven ‘Engineering precisely what you value’ philosophy, our relation with Metalex evolved by looking at various solutions and machine types available under the Starrag portfolio,” continued Quack. “Together we arrived at the Droop+Rein T series, a portal milling machine that offers superb rigidity, essential for highly-accurate machining. We added the two rotary tables and the turning tool holders for in-cycle turning operations, and expanded the horizontal and vertical clearance to suit.”
Quack confirmed, “With no comparative workpieces, from the outset we knew that Metalex wanted a machine that would meet all eventualities and, as always, Starrag applied the best world-class technology solutions including Balluff tool identification, Renishaw probing, BLUM laser tool measuring, video monitoring of the work area using four cameras, ARTIS tool and process monitoring and Brankamp collision monitoring all integrated via the machine’s Siemens 840 D SL CNC system.”
The machine is due for delivery in 2020 and production is scheduled to commence in 2021.
Kevin Kummerle, CEO of Metalex, summarizes the pre-order project phase by saying, “For Metalex to continuously evolve and be a company of the future, a combination of our capabilities, technology and people must work together to create innovation that sets us apart from others. Our customers need to know that their key suppliers are committed to be at the leading edge of their industry offering the best total value in terms of quality, technology, cost and service for today and for the long run.”
“Metalex applied these same considerations in their evaluation process,” said Kummerle, “looking for a partner that could provide a complete technology solution for our application; a highly flexible and accurate machine configuration integrated with the latest in technology supported by a service organization capable of rapidly solving challenges that arise. All of these factors are why Metalex selected Starrag as our partner on this critical project.”
About Starrag
Starrag Group is a global technology leader in manufacturing high-precision machine tools for milling, turning, boring and grinding workpieces of metallic, composite and ceramic materials. Principle customers are internationally active companies in the Aerospace, Energy, Transportation and Industrial sectors. In addition to its portfolio of machine tools, Starrag Group provides integrated technology and maintenance services that significantly enhance customer productivity.
The products are marketed under the brand Starrag and include the product ranges Berthiez, Bumotec, Dörries, Droop+Rein, Ecospeed, Heckert, Scharmann, SIP, Starrag and TTL. Headquartered in Rorschach/Switzerland, the Starrag Group operates manufacturing plants in Switzerland, Germany, France, the UK and India and has established a network of sales and services subsidiaries in the most important customer countries.
Starrag Group Holding AG is listed on the SIX Swiss Exchange.