When home appliance, aka “white goods” manufacturers need to shred defective oversized sheet metal or component parts prior to shipping for further recycling or re-use in production, the only option traditionally has been hydraulically powered, due to the high torque and power delivered. Although this is important for oversized parts, thick-gauge metals, and other hard materials, it is overkill for the light-gauge mild steel, sheet metal, and plastics used to manufacture most home appliances.
Enter electric powered shredders with design advances that can deliver the necessary torque and chamber size to quickly shred bulky, recyclable materials as used in the largest home appliances.
For white goods manufacturers, electric power offers some key advantages over hydraulic power. To start, electric shredders are generally less expensive than comparable hydraulic units. Electric shredders also eliminate the maintenance and inspection associated with hydraulic systems, namely fluid leaks and ruptured hoses. By eliminating hydraulics from the equation when large cutting chambers are still needed, facilities ensure a cleaner, safer work environment and prevent the potential slip and fall hazard represented by leaked hydraulic fluid on the plant floor.
Electric shredders are also much quieter. This lowers the noise level in decibels in already loud facilities. Consequently, it is easier for workers to communicate without having to shout over the loud background noise of operating machinery. The quieter operation of an electric unit also facilitates compliance with OSHA’s permissible occupational noise exposure limit.
“Appliance manufacturers that recycle oversized products constructed of light-gauge steel and plastic have expressed a preference for large chamber, electric shredders that are quieter, eliminate the potential for hydraulic fluid leaks, and cost a bit less,” says John Neuens, Industrial Consultant for Milwaukee, WI-based BCA Industries, an established developer and manufacturer of industrial shredding and recycling equipment for a variety of industries.
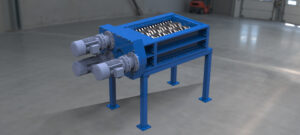
Designed to handle large, bulky recyclables like home appliance metals and plastics, electric shredders like those from BCA Industries are cost effective, quiet, and eliminate the potential for hydraulic fluid leaks.
Although electric shredders provide slightly less torque than hydraulic models, those designed to handle large white goods and other bulky recyclables can still deliver more than 100,000 ft. lbs. of torque per knife.
“Applying over 100,000 ft. lbs. of torque per knife in a large chamber is more than enough to efficiently shred sizeable, defective white good materials from stoves, refrigerators, freezers, washing machines, tumble driers, dishwashers, water heaters, and air conditioners,” says Neuens.
He points out that one electric-powered unit, the customizable ES2000 shredder called “The Beast” from BCA Industries, is already being successfully used by the appliance division of a major global OEM at a facility in the U.S. Midwest. At the facility, the OEM is shredding bulky, hard to feed, substandard or defective appliance parts into small one-inch pieces and then transporting the scrap by rail to their recycling division.
With chamber sizes from 48” x 48” up to 48” x 72”, the electric shredder provides from 100 HP to 800 HP and 100,000 ft. lbs. of torque per knife. This is more than enough size and power to quickly reduce defective oversized items into easily transportable, recyclable scrap.
According to Neuens, BCA Industries designs the electric shredder to many of the same specifications as its hydraulic models to maximize durability and longevity in the field.
“We designed the electric shredder to be extremely durable even if the intended use is lighter duty metals and plastics, in the event the manufacturer pushes the envelope of what feed materials are placed into it in the future,” says Neuens.
For example, the electric shredder is designed with 24” AR500 base alloy knives with a hard-face weld, the same as the hydraulic alternative. The knives can be selected in a wide variety of sizes and specifications, which allows customization to suit the manufacturer’s specific application.
Several features are designed to increase the electric shredder’s useable life and reduce maintenance. Instead of 7” shafts, 8” chromoly shafts are utilized – the same as the hydraulic unit. In place of old HEX shaft design or a double key round shaft, the unit also uses an eight key design where the knife literally rides on disposable keys, not directly on the shaft. With the keys taking any abuse instead of the shaft, the design eliminates shaft washout and simplifies knife changes.
Since the electric unit is designed with a double labyrinth style drop zone and outboard bearings, this eliminates any direct path to the shaft bearings. It also allows compressed material a path to exit the shredder, eliminating the “catastrophic costs” of bearing and shaft replacement.
To expedite scrap reduction to the appropriate specified size, the electric shredder offers the option of BCA’s patented Triplus system shredder “knife” technology. When used in the shredder, the knife technology can uniformly cut to any size in a single pass without a screen to quickly reduce scrap to a reclaimable proportion. The technology utilizes a unique bed knife design in a dual shaft shredder to cut the width of the material of the shredder. The size of the end-product is based on the size and geometry of the rotary and fixed knives as well as their gap distances.
A shredder using this design can produce over 85% correctly sized material in one pass with less than 10% oversized material, according to Neuens. He notes that the knife system can reduce scrap to the appropriate size with much less energy than typical shearing and grinding equipment. Power efficiency approaches 150% over any standard shredder.
Large chamber electric shredders are also easy to use for plant operators. The latest offer touch screen programmable functions and diagnostics and are PLC controlled with auto-reverse and overload protection.
“Manufacturers of oversized product that needs to be recycled finally have an electric-powered option that makes shredding onsite much easier, quieter, cleaner, and cost effective,” concludes Neuens. “Although hydraulic power has been the default choice, large chamber, electric-powered units are an attractive alternative for home appliance manufacturers, bulky industrial tubes, gas tanks, plastic totes and barrels, laser skeletons, and most other recyclables.”