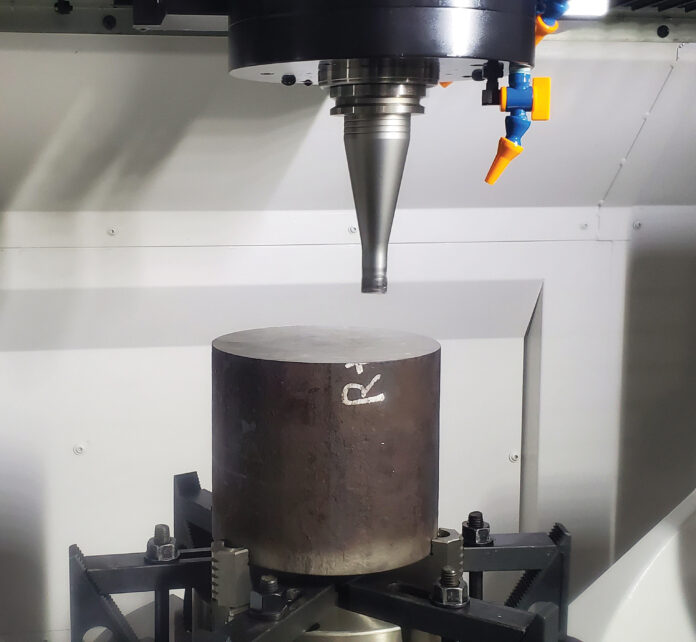
According to the Association for Manufacturing Technology (AMT), orders for 5-axis machine centers grew 22 percent year over year—in the middle of the pandemic. Machine shops represent nearly half of all buyers. What those shops understand, or learned quickly, is that getting the most out of 5-axis machinery requires a little different approach; factors like holder interference, productively reaching into deep work envelopes and high-mix part changeover are just a few that come to mind.
What can you do about it? How should you think differently? What equipment do you need if you’re adding a 5-axis? We have some answers.
Material sourcing
Let’s start with one of the most fundamental steps of making a part before we’re even thinking about machining: which material to source. Yes, 5-axis work can even be a little different here. Here’s just one scenario.
While a square or rectangular billet will save some time when they resemble the shape of the finished part, the movements a 5-axis machine allows, provide more options. There are hidden savings to be found. Bar stock is less expensive, more readily available, and easier to hold than more frequently used billets. The material savings and ease of purchase will probably far outweigh the up-front cost.
Getting organized
You’re in a higher stakes game with 5-axis machining. Don’t overlook your tool lists. Since the risk of collision is higher with 5-axis work, you should be using accurate 3D models of every tool holder in your CAD system. Body diameters, gauge lengths, etc., in CAD should be as close as possible to how it will be put into the spindle.
Do as much of this offline as possible; keeping spindles spinning is one of the best ways to realize return on your machine investment as soon as possible. Plus, using a ruler with 1/16 increments, trusting every spec or using inconsistent in-machine probes are not effective ways to measure when a couple of thousandths can make a difference like they often do in 5-axis machining.
Tool presetters are a great tool for performing those measurements away from the machine, but they go far beyond simple measuring these days too. Presetter data can be connected to broader tool management systems and/or machines. They are the ideal setting for assembling tools and comparing them directly to a catalog, DXF or STP model given to the programmer.
If adjustments do have to be made at the spindle, digital heads have on-tool readouts that make it easy for operators to see and make extremely precise diameter adjustments. A corresponding mobile app allows for fast lookup of tool speeds and feeds on the spot.
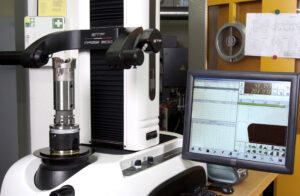
Holding parts
Workholding can play a huge role in making different jobs easier or even possible. For starters, being forced to match a workpiece and fixturing to the standard round, square or rectangular table or plate can be difficult when angles and tool approach are important and parts are high mix.
Initially developed for setup-time reduction, zero-point workholding has evolved and proven valuable for another distinct reason: access. Systems like the UNILOCK offer the added flexibility that’s valuable in 5-axis machining on a new machine.
For example, while standard vise blocks the sides of a part and low-profile vises leave sides more open, they only grip only along the part’s lower edge. Zero-point workholding offers the option to clamp exclusively on the underside of a part for a freer state of machining and concealed from all interferences.
5-axis workholding is a complex world. There is no one-size-fits-all answer. Here’s our bottom line for selecting workholding:
- Find a balance between stability and access.
- Know what parts are coming next, how finished they are, basic size and shape, etc.
- Choose the best chuck for the work you do and lay it out carefully.
- Plate material and thickness are key when using multiple chucks.
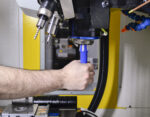
Holding tools
The ultimate goal is to make every tooling assembly, especially in 5-axis machining, as short as possible. The shorter the tooling, the less room for error. That said, the unusual angles, sizes, and shapes of the parts that require multiple axes don’t always allow for that. We’ve talked about some workholding solutions for this challenge, but you have options in tooling selections too.
The choice for 5-axis access often comes down to hydraulic chucks and shrink-fit holders. Compared to collet chucks, shrink-fit holders and hydraulic chucks are able to maintain higher rigidity and accuracy and have a smaller nose diameter relative to the tools they hold. This allows a further reach into mold cavities or other tricky work envelopes without interference.
If you’re deciding between hydraulic chucks or shrink-fit holders, you’ll likely pay less for shrink fit holders upfront but maintaining the heating and cooling systems will require maintenance and training hours over time. These temperature cycles do add to setup time as well.
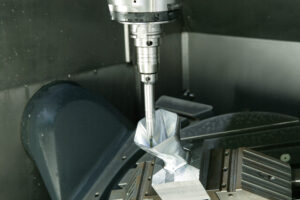
Maintaining performance
We’ve talked about the importance of precision when you’re moving on so many axes. Each point of contact should also be kept clean to maintain performance, i.e., avoid scrap or poor finishes resulting from misalignment or chatter. These contact points include the spindle taper, clamping bores and, in the case of BIG-PLUS tooling, both the taper and flange mating surfaces of the dual-contact system. It’s tedious, dirty and even a little dangerous when chips are involved.
That’s why you can’t overlook the tools out there for keeping your equipment in good working condition. These minor investments may be the last thing on the mind of a shop owner with a new 5-axis machine, but it will certainly pay big dividends if deployed right away. Here are just a few examples:
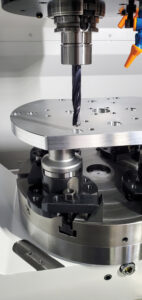
Bore cleaners remove chip particles, grease, oil, and coolant from the hard-to-reach clamping bores of milling chucks, hydraulic chucks, and shrink-fit holders.
Taper cleaners serve a similar purpose at the other end of the tool, ensuring clean clamping into the machine spindle.
Gages, like our Dyna Contact, make verifying taper tolerances simple. All the operator has to do is apply blue dye to the ceramic gage, insert it in the machine spindle and remove it. A quick visual check will reveal any improper contact.
It’s inevitable that particles and residue find their way into a machine tool spindle. This not only makes it harder to dial in cuts and harms tool life, but it can also damage spindles over time. Spindle cleaners keep this issue under control.
The addition of a 5-axis machining center is a big deal for any metalworking operation. Apart from the financial commitment, it changes how jobs move through the shop and the way people work. Similarly, don’t assume the way things were done on an older machine is the best way. Getting creative and seeking out inventive solutions designed for 5-axis work—even if it’s just an inexpensive accessory—can accelerate all-important ROI, empower the team to succeed and unleash the full capabilities of the business.