
Speeding up laser cutting production sounds great in theory—and today’s technologies make it even easier to increase productivity and throughput. But when upgrading equipment, fabricating companies don’t always see the pitfalls—and sometimes fail to adjust their processes accordingly.
The downside of faster production can become especially evident for companies that operate in a high-mix, low-volume manufacturing environment. The perceived gains from faster cutting speeds are quickly diminished when parts sit as ‘work-in-process’ immediately after cutting. When lasers begin to outperform the offloading operation, the bottleneck shifts to parts organization—and shops must adapt accordingly. Because of this, it’s crucial to think beyond the cut.
Start at The End
Starting with the last process and working backward is a good way to identify inefficiencies and opportunities for cost reduction. For instance, if you find that parts are getting lost as they move from one stage of the production process, it may make sense to switch to kit nesting during the cutting process, so the parts that need to end up together stay together. In this scenario, automated parts sorting could be beneficial for increasing manufacturing velocity through each stage of the process.
Understand the Real Costs
Not all processes are created equal in terms of costs. So identifying individual process costs is the first step toward understanding where the greatest savings can be made. You might be surprised to learn that while blanking receives the most attention in the average shop, it actually is the least costly of all the value-added processes required to make a completed weldment or assembly. In fact, bending is associated with a much greater cost. Automated part sorting can offset this by reducing work-in-process prior to the bending operation. Furthermore, parts could be sorted into stacks according to grain direction to minimize errors during the bending process.
Address Non-Value-Added Time
Actual processing time is a small percentage of the overall time required from when an order is received until it is shipped to the customer. The low-hanging fruit for most fabricators involves addressing costs associated with non-value added time before and after the actual processing time. The goal is to identify the costs and eliminate the issues in both front-end and downstream processes by implementing a solution that can be used to maximize manufacturing velocity.
Solving the Issues at Hand
Once you have a good handle on the bottlenecks in your process, it’s time to think about ways to address them. Automated solutions are gaining popularity because they are becoming easier to use and integrate. They not only address issues related to the skilled labor shortage, but alleviate issues that hamper productivity and cut into profit. In fact, integrated multifunctional laser automation systems now exist, capable of controlling the entire production process from loading, cutting, sorting, and unloading through to the storage of the finished parts. Here are some ways this type of technology can help.
Save Time on Sheet Positioning
Automated systems that employ aerial positioning can save 20-30 seconds a sheet during positioning. They use pneumatic blocks that move against the edges and square the sheet to a known location—with no need for additional position adjustment.
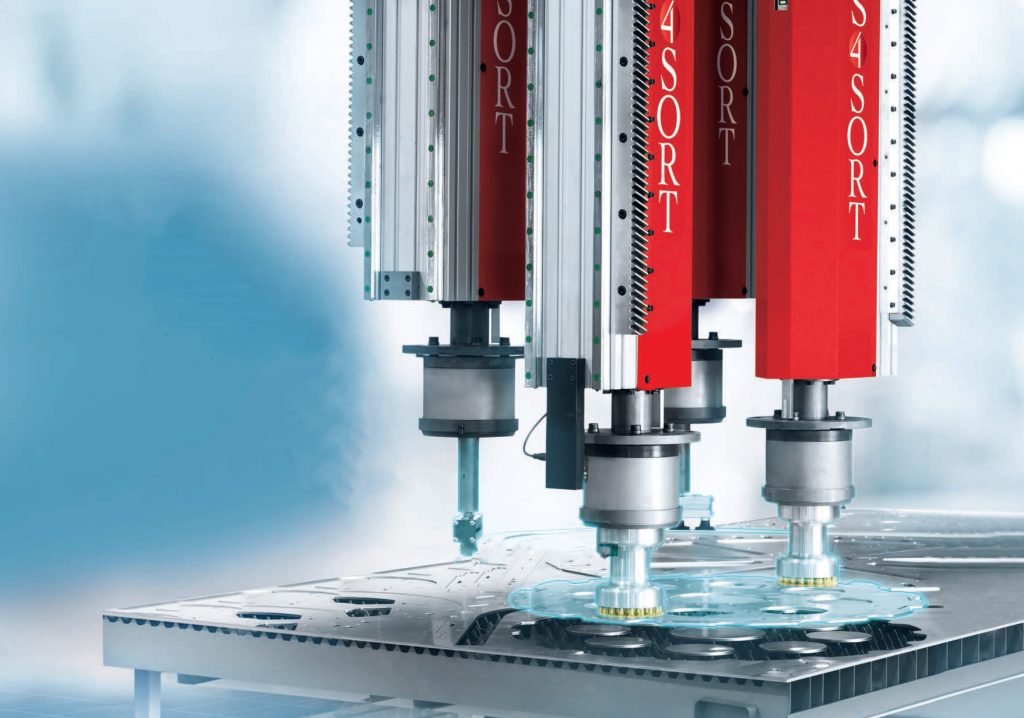
between the laser and the sorting mechanism
Ditch The “De-Nesting Party”
Are you stopping production to have “de-nesting parties”? This manual, time-consuming process of removing cut pieces from the skeleton by hand can be a major liability. Not only can it lead to sorting mistakes and loss of parts (and profit), but it can also be downright dangerous. Thicker sheets, in particular (1/2- to 1-inch sheets) can be difficult to extract, and workers often engage in dangerous practices—like using pry bars and even 2x4s to facilitate extraction. Automated systems can solve these issues—especially those capable of handling heavy weights with heavy-duty gripper heads.
Avoid Part Damage
During de-nesting (either manually or via automation) damage and tangling is always a possibility. To avoid this, parts should be lifted straight out of the skeleton, with parts gripped as close to their center as possible. Systems with more vacuums or magnets offer more granular locating, which contribute to an efficient, problem-free de-nesting process. Another issue that can hamper de-nesting is the flatness of a sheet. If the sheet warps, the edges can get caught or the center of mass can move, resulting in damage—an issue that’s difficult to predict or prevent. Some advanced automation systems, however, can notify operators of problems with de-nesting/picking, before the problem results in a large volume of scrapped parts.
Sort Like A Pro
Automation systems can facilitate more efficient, accurate sorting—a boon for productivity and profit. Be sure, however, that you’re picking a fully integrated system with an arm and tooling that can both support the weight, size, thickness and material of the parts.
Final Considerations
Keep in mind that the integration of automation may require some adaptations to the way you cut. For example, automation requires more rigidity around the edges, since automated systems can’t adapt to de-nesting issues in the same way humans might. Parts may need to be cut so that they are tabbed in, and acute or sharp edges can cause issues. Complex cuts or sharp edges may require creative cutting—like cutting a circle around the part for easier automated picking, then using additional processes to remove the piece inside. Some smart software programs that integrate the laser and the automation equipment can help the user program cuts that make the parts easier to extract. Talk to your laser automation rep for additional tips on how to adjust your cutting processes to better accommodate automation.
A Powerful Solution
MC Machinery offers a new solution to laser automation: Lasorting—the first fully integrated sorting and cutting system. This system, known as the ASTES4, features patented SortCAM software that provides seamless communication between the laser and the sorting mechanism. The system can detect the material being cut, the thickness and even where the parts are on the sheet. This data is transferred to the ASTES4 and converted into a sorting plan.
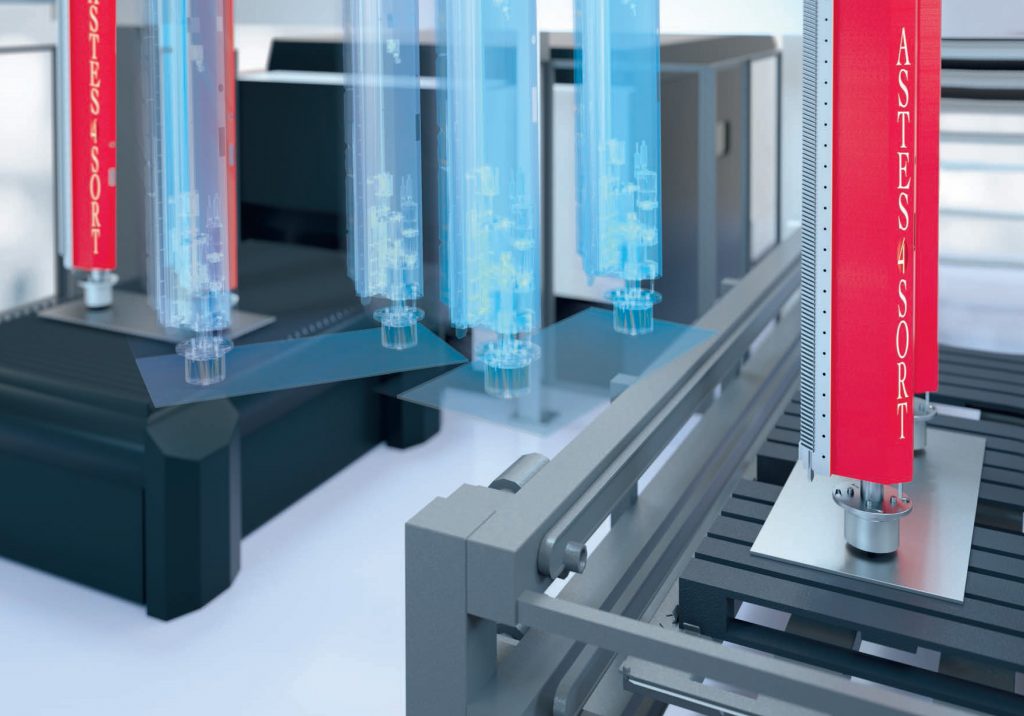
The ASTES4 system helps shops find real efficiencies while eliminating error and injury. Some key features and benefits include:
- Two gantries, each with two gripper heads, can use a vacuum or magnet, depending on the nature of the piece/cuts; combined capacity is 4,400 lbs. for the traditional system and more than 10,000 lbs. for the heavy-duty version.
- A Cartesian gantry system with X/Y axes and a Z can lower a magnetic or vacuum gripper to collect and, if necessary, rotate parts up to 360 degrees for placement in a known location for easier sorting.
- The system can be equipped with a printing head for easy labeling and sorting.
- Patented SortCAM software (included with the system) provides seamless communication between the laser and the sorting mechanism.
- The software also provides tools to help users program laser cuts for easier removal or sorting—on parts with jagged edges that are hard to extract, for instance.
- MC Machinery has plans to integrate the ASTES4 with its Remote 360—a remote laser monitoring application—so operators have 24/7 visibility from anywhere.