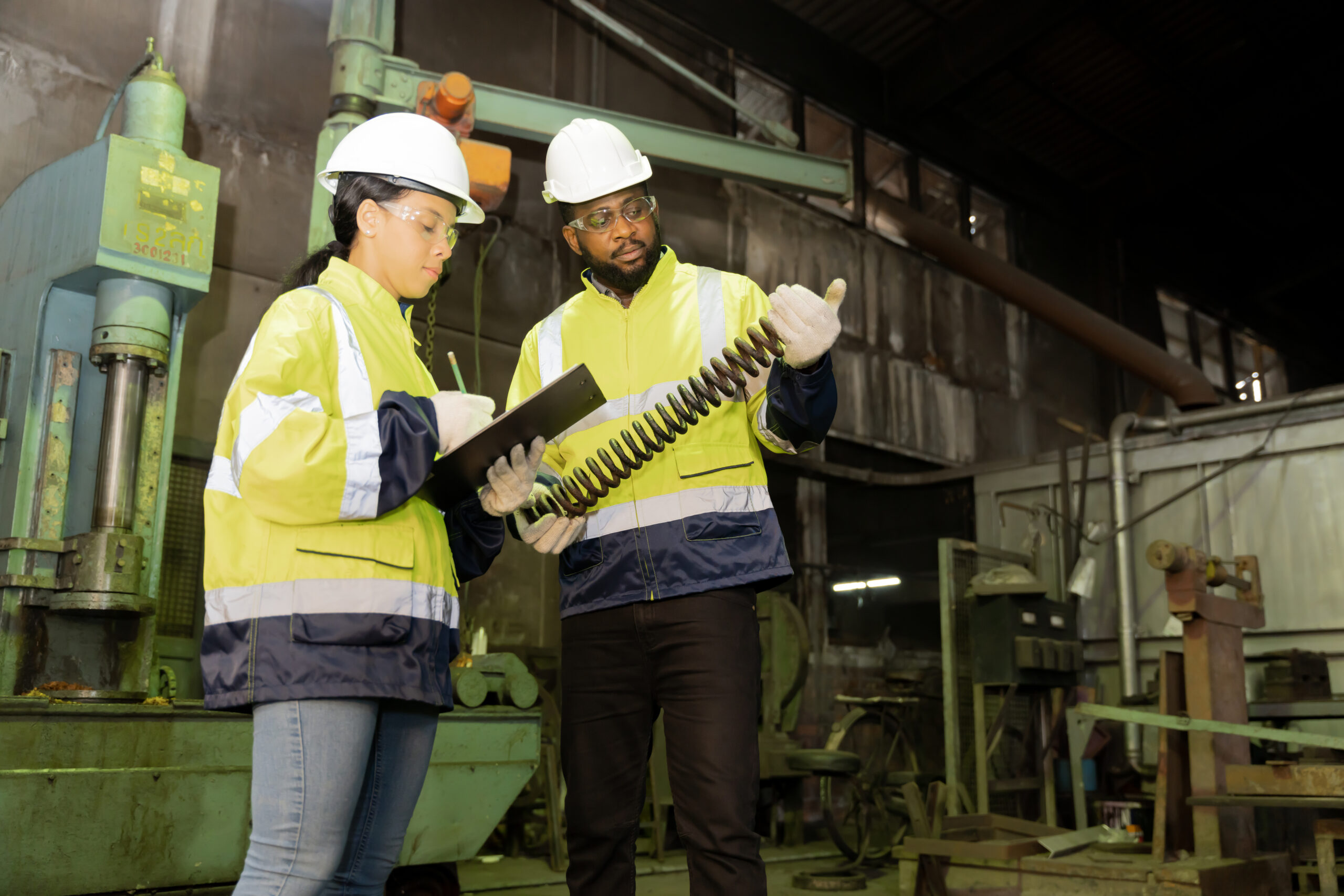
Preparing for an OSHA inspection may seem daunting, but a proactive approach can ensure smoother navigation of the process. Occupational Safety and Health Administration (OSHA) inspections are designed to ensure workplace safety and minimize hazards. While they can feel disruptive, these inspections also offer valuable insight into areas that need improvement. With the right preparation, employers can protect their workforce and avoid costly penalties. Here’s a comprehensive guide on the critical steps to manage an OSHA inspection effectively.
Why OSHA Inspections Matter
OSHA is dedicated to maintaining safe workplaces, and inspections play a vital role in enforcing this mission. Companies in high-risk industries, those with recent complaints, or workplaces where severe injuries have occurred are among those most likely to face an OSHA inspection. Beyond the immediate implications of an inspection, keeping workplaces in compliance with OSHA standards significantly reduces the likelihood of injuries, improves morale, and even enhances productivity.
Preparation Is Key: Laying the Groundwork for a Successful Inspection
Review and Organize Documentation A well-maintained record of safety documentation is the foundation of a strong inspection process. OSHA mandates that employers keep accurate records of workplace injuries and illnesses, including OSHA 300, 301, and 300A forms. Ensuring these documents are current, accurate, and easily accessible demonstrates a commitment to compliance and can make a positive impression on inspectors.
Ensure Training Compliance Safety training, especially on OSHA-regulated topics like hazard communication and personal protective equipment (PPE), is essential. Keep a log of training records that includes dates, employee names, and the content covered. OSHA inspectors will assess these records to verify that training is thorough and frequent enough to mitigate known risks effectively.
Conduct Routine Safety Audits Regular safety audits offer insights into potential hazards and ensure that corrective measures are taken before they escalate. Forming a safety committee or assigning a safety officer to oversee these audits can foster a culture of proactive safety management. Documenting these audits and their findings is equally important, as OSHA inspectors may review these records as part of their evaluation.
Prepare for the Inspection with Mock Walkthroughs Conducting a mock OSHA inspection can identify areas for improvement and highlight any gaps in safety practices. This exercise not only ensures compliance but also familiarizes team members with the inspection process, minimizing stress when an actual inspection occurs.
Understanding the Inspection Process
When an OSHA Compliance Safety and Health Officer (CSHO) arrives for an inspection, they will typically begin with an Opening Conference. In this phase, the CSHO explains the purpose of the visit, which may be scheduled or unannounced, depending on the circumstances. For instance, inspections related to severe incidents or imminent dangers are often unscheduled to capture real-time practices.
Request Identification and Verify the Scope of the Inspection Politely ask the CSHO for identification and ensure their credentials are in order. Once identification is confirmed, clarify the inspection scope, as some inspections may focus on specific hazards, while others may be comprehensive. Designating a company representative to handle communications with the inspector helps maintain organization and control over the inspection process.
Define Internal Roles and Responsibilities Assigning specific roles—such as a point person to accompany the inspector and a record-keeper to document the inspection process—helps ensure that key aspects of the inspection are handled promptly and accurately.
The Walkaround: Ensuring Compliance in Real Time
During the Walkaround Inspection, the CSHO will tour the facility, inspecting specific areas, equipment, and work practices. This stage is critical, as it provides the most direct insight into OSHA’s evaluation of your workplace.
Document the Inspector’s Movements and Observations During the walkaround, your designated company representative should take detailed notes on every area inspected, equipment observed, and any specific safety practices noted by the inspector. Photos can also be valuable for your records, particularly if the inspector highlights areas of concern.
Display Normal Working Conditions Ensure that work operations during the inspection reflect typical conditions rather than adjusting or halting activities. This approach demonstrates transparency and adherence to safety standards as they are practiced day-to-day, which can work to your advantage.
Limit Access to Confidential Areas OSHA allows employers to mark certain areas as confidential if they contain sensitive information or trade secrets. Discuss these designations in advance and inform the inspector of any restrictions, while still accommodating the needs of the inspection.
Handle Employee and Management Interviews with Care Inspectors often interview employees during the inspection process. To facilitate these interviews:
- Educate Employees on Their Rights: Inform employees that they have the right to request a representative, refuse recording, and answer questions without speculation. These interviews offer employees a chance to share their experiences openly, and educating them about the process beforehand can promote a constructive atmosphere.
- Debrief After Interviews: After the interviews, consider holding a brief meeting with employees to review topics discussed, which helps maintain alignment across safety practices.
Addressing Findings in the Closing Conference
Following the walkaround, the inspection concludes with a Closing Conference. During this phase, the CSHO will discuss any preliminary findings, answer questions, and clarify possible violations.
Seek Clarification on Any Observations or Citations It’s essential to ask questions and fully understand any citations, associated standards, and the nature of identified issues. Taking detailed notes during the conference will be valuable if further action is required.
Request Additional Time for Follow-Up If the inspector requires additional documentation or corrective actions, confirm a timeline for follow-up. This request provides a clear path for remedying concerns and completing outstanding requirements.
Post-Inspection: Follow-Up and Record-Keeping
Once an inspection concludes and any citations have been issued, OSHA requires employers to post citations in a visible area within the workplace for at least three days or until the cited issue is corrected. This posting period offers transparency and helps reinforce accountability.
Establish a Corrective Action Plan For citations that require action, creating a corrective plan with clear timelines, assigned responsibilities, and specific steps can ensure timely completion. Document every step taken to remedy each issue, as this information may be reviewed in future inspections.
Document All Follow-Up Actions Each action taken should be documented and stored for future reference. A comprehensive record not only aids in verifying compliance for future inspections but also supports continuous improvement in safety practices.
Maintain an Ongoing Compliance Program Implementing an ongoing compliance program ensures long-term adherence to OSHA standards. Regularly reviewing safety protocols, updating training programs, and conducting frequent audits are key to maintaining a safe work environment. For companies facing recurrent inspections or those in high-risk industries, such measures can significantly reduce the likelihood of future citations.
Leveraging Technology for Compliance Management
Digital tools can streamline OSHA compliance by centralizing safety documentation, tracking audits, and simplifying incident reporting. Companies like VelocityEHS offer solutions that help automate many compliance-related tasks, enabling efficient management of safety protocols and providing real-time data insights. Solutions like VelocityEHS not only support compliance but also empower employers to proactively address safety issues before they result in incidents or penalties.
In Summary
Successfully navigating an OSHA inspection comes down to thorough preparation, clear communication, and responsive follow-up. By maintaining up-to-date documentation, conducting regular audits, and fostering a culture of safety, organizations can minimize disruptions from inspections and focus on long-term improvement. Every step taken toward compliance is also a step toward a safer, more efficient, and productive workplace.