Glen Betenbender began his career as a blacksmith in Coggon, Iowa in the 1930s. During WWII, he ran a small fabrication and repair shop. In 1948 he and his wife moved their growing business into their current location as a repair and manufacturing facility. Their son, Max, joined the company in 1967 after serving in the United States Army.
In 1972, Glen or “Pete” as he was known to his friends, ran a construction company as well as a farm with livestock. He was having to build chutes that load cattle into the back of pickups. As part of his process to get the material sheared for the chutes, he would travel to Cedar Rapids or Marion. These were the closest locations that had equipment to shear his metal. On one of the trips he studied the shear and decided he could make one himself. After gathering some old farm implements, some hydraulic cylinders, a used log splitter valve, and a pump that was lying around, he began welding. He made the first “A” shear for their family’s own use. In the small town of Coggon though, word traveled quickly about a farmer that was doing something which was faster than everyone else could. Then he got a request to build one locally for someone that needed it. Shear #2 was out in production, and further demand from other local businesses for their shear prompted the Betenbenders to begin producing shears for nationwide and international resale.
Matt Enos, Plant Manager at the single Betenbender manufacturing facility in Coggon, Iowa says, “I’ve actually worked on Shear #2. It’s still operational today,” with a lot of pride in his voice, “and they tell me that the first one is still operational, but I don’t know where it is. But I know that Shear #2 is sitting in Wadena, Iowa, and it’s still being used nearly every day.”
Pete’s son Max joined the business after he’d been serving his country in the US military for a short while. Says Enos, “He was really good with design. He was good at making improvements to the machines.” Both men stood for American ingenuity and commitment to delivering value with every unit. In 2009, at 86, Pete passed. 10 years later in 2019, at the age of 73, Max passed away.
If It Ain’t Broke, Don’t Fix It
Matt Enos will be celebrating 29 years with Betenbender Manufacturing, Inc. in October of this year. He counts himself as one of the average lifers that are there. “There are I think 5 people here that have been here longer than I have.” I asked him how he would characterize the culture at Betenbender. “It’s good. It’s somewhat laid back. We don’t have people screaming at one another or anything like that. It’s a positive culture.” Certainly this culture must have been passed down through the generations. Strong-willed companies that survive countless economic cycles, changes in economic policies, advances in manufacturing, changes from just-in-time to six sigma to lean manufacturing philosophies, and global pandemics don’t just happen overnight. “The wife of Max (Donna) and his daughter (Teresa) are active owners. They come in from time to time. Teresa is here about three days a week, while Donna stops in briefly every day. There’s also a cousin, Gene Betenbender. He’s been here for about 28 years.”
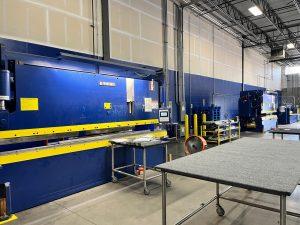
Culture has remained consistent over time and so has the recipe for building machines. Grit, determination, tried-and-true approaches are all part of the combination to build the most durable press brake on the market. While getting their start in shears, Betenbender has a broad offering of press brakes. Enos answers a leading question I ask him which is “Do you use any special sensors? Do you have anything on the digital front that you see is changing how you’ve approached the market over the last few years?” His response is pretty straightforward, confirming my theory. “We’ve stayed pretty steady over the years for that, in the gauging process of our press breaks. We offer the very basic back gauge, which is just a hand wheel on the back gauge that moves back and forth. You have a little readout that’s our very basic back gauge and we also have all the way up to a full CNC. We use Automec out of Waltham, Massachusetts for our CNCs and that offers 150-300 jobs, 10 bends per job, and that allows you to complete multiple bends. So make a part that has multiple bends and it keeps repeating over and over.”
Enos took me through an example of the press brake and educated me on the 550 ton units to the “smaller” 190 ton and 50 ton units. For me the numbers sound a bit staggering. “What’s an example of where I would see a 550 ton press brake?” Enos says “CVA, Cryogenic Vessels out of Baytown, Texas. They build big tanks that hold liquid oxygen or liquid nitrogen. They bought an inch and ¼ shear, and I believe they bought a 550 ton press brake.” Having gotten a bit of explanation on the machines and knowing they are using a metal sheet, I go on to ask him to explain to me what they are doing with that piece of metal in general.
He explains, “For their shear, they’re just trim cutting, or squaring it up so they can run it through their roller system. They’ve got a very large roll so they can roll the metal around and then they can weld it up using a robotic welder. Other companies that have our large press brakes they’re either just forming V’s, or some of them are using them to punch. A lot of times we team with places like UniPunch where we will set up a whole series of hole punches in our press brake to form parts. These other companies like UniPunch will set up a series of their unitized punches. We did one for Winnebago Industries, probably 15 or 20 years ago.” He was now talking RVs, something to which I could relate, having owned one for a minute. I knew Monaco and I had looked at Winnebago coaches as well. “At Winnebago, a very large manufacturer of RVs, they had a lot of aluminum parts on their coaches that were 16 feet long. We built two eight foot press brakes, put them side by side so they come down at the same time and they punch holes in that aluminum piece, a whole series of different holes so they can put their rivets or fixtures in there,” said Enos.
Betenbender has such a large range of offerings from large tonnage, to the workhorse 190 ton, to even the smaller 50 ton. Matthew explained when the smaller ones would be needed. “Let’s say someone calls and tells us they need a press brake that will bend ten feet of ¼” material. That’s a common one. We have a tonnage chart, but I’ve been here long enough to know that it takes 15.4 tons per foot to bend ¼” milled steel over a 2 inch V-Die. I’ll do that math to come up with 10x 15.4, which would be 154 tons. We could provide a 160 ton press brake for this job. But generally it’s best to stay at around 80% of the capacity of the unit, so we would sell the 190 ton press brake for this job.” Staying in the 80% capacity range is to compensate for a batch of steel that may be harder one day due to any number of material properties specific to that batch. And as the gauge thickness of the steel changes, of course the tonnage per foot of bending changes. Also, the machines can be designed for specific widths of material as well. Enos said the smallest press brake was a 4’ by 50 ton.
After learning about the press brake capabilities, I asked Enos about change.. “Something has to have changed in the design. What’s changed? Has it continued to be the same for the last 10-15 years?” I asked.
“We’re building a very similar product to what we were building 28 years ago. We’ve added a few things and improved a great deal. We’ve gotten better controls and better hydraulic setups. We’ve switched flow dividers, probably 15-20 years ago, so our machines are even more accurate. We switched to ball screws back in the late 90s for our back gauges, so that added much more accuracy on the back gauge. But really, if you had a machine that was from 1998, and you sat it next to one that was built today, you wouldn’t be able to tell the difference. You wouldn’t be able to tell me which one was the new one. It’s pretty much the same.”
Shear Perfection
Enos went on to tell me about the shear and how it uses a type of guillotine action for the cut. There are a lot of options that can be modified on the shear, including blade distance, angle of cut and others. The blades, made of high carbon high chrome alloy, come down more like scissors than a guillotine, and they run across each other without touching. Generally there is a three to twenty thousandths of an inch gap depending on the type of material being sheared.
“Especially over the last 15 years,” said Enos, “the only thing we’ve done differently with the shear of substance, is we’ve gotten the go-to controller. Now we’ve added a touch screen controller for the back gauge, but really it’s the same hydraulic system. Our thought on that is that it works. Why do we need to change it? The customers like it, our team is used to building them that way. Let’s keep doing it.”
The Rest is History
Make no mistake though, Betenbender has maintained a strong market position and focused on seizing opportunities – and that includes timely acquisitions. In 2012, the company purchased Hydraulic Machines, Incorporated which was a family owned business as well. The company owners of Hydraulic Machines were friends with the Betenbenders (who actually had a couple of their machines in the Coggon facility) and approached them about a sale. Now Betenbender has a product line called Hydraulic Machines of Iowa to provide C-Frame presses or punches.
From the C-Frame presses, to the shears, to the press brakes, to the hydraulic punches, Betenbender is made in the USA and has withstood the test of time with standard offerings. That doesn’t mean the need for customizing for a client requirement doesn’t happen. “Back when Max was alive, he’d go out on to the floor and he literally would grab a piece of chalk and start chalking out customizations on the floor, how he wanted to redesign something, or he would take a piece of steel and draw it out on that plate and say, ‘Here, cut this,’ and we’d cut it and off we would go with the customization.”
To this day, they keep the same view. Build strong, durable equipment that completes the customer’s job, and treat every call for support and every issue as one that needs solving now. Says Jason Stayton, General Manager for Stafford-Smith’s Arlington Texas location, a Betenbender customer since 2021, “After reviewing the machines personally, we knew they were a great fit for our fabrication industry. The CNC controls and back gauge make it user friendly. The shear and press brakes we have make precise cuts and bends to form our custom stainless steel kitchen equipment.” Somewhere Max and Pete are smiling. Another happy customer. Another precision job well done.