In 2019, strategy consulting firm McKinsey & Company published a perspective called “Changing Market Dynamics – Capturing Value in Machinery and Industrial Automation” which took a look at the multi-trillion dollar industrial automation industry and noted the driving groups providing Industry 4.0 capabilities could be broken into 3 main categories of businesses:
- OEMs and System Integrators – manufacturers of machines and robots, and integrators of their own and other’s products into customer-specific lines or cells;
- Component Suppliers – automation suppliers who provide actuators, HMIs (Human Machine Interfaces), sensors, as well as suppliers of control systems such as PLC (programmable logic controllers) and DCS (distributed control systems), and non-automation suppliers for items that “glue” everything together such as wires, cables, housings, and bases;
- Software, Platform, and Application Providers – management software providers, providers of process/plant / enterprise management software, providers of IoT platforms, IoT platform providers for third parties, (cloud) data storage providers and services, business application providers, developers of business applications, e.g., and predictive maintenance solutions.
A survey of the providers of these capabilities, and a look at the largest players in these spaces, revealed a couple of roadblocks to achieving Industry 4.0 digitization. First was that “nearly three-fourths (72 percent) of the machinery and industrial automation players surveyed indicated they did not yet possess all of the requisite digital capabilities.” Second roadblock was that it was difficult for these providers to establish clear and profitable business cases for digitization.
The very next year, in 2020, global consulting firm Accenture published “THE RACE FOR DIGITAL OPERATIONS TRANSFORMATION- the time for experimenting is over” in which they surveyed users of Industry 4.0 capabilities (in the McKinsey published research, the survey was focused on the providers in each category). It has been well over a decade since the vision for Industry 4.0, essentially the digitization of manufacturing, was evocatively touted at a trade fair in Germany (Hannover Messe). Accenture’s survey of over 600 companies assessed the maturity levels across a stack of 40 key digital capabilities, and concluded the average digital maturity for deployed capability was only 39%. Based on the research, this meant that many of the respondents had simply piloted several of the key capabilities (the survey goes on to identify the 11 top digital capabilities actually deployed).
Building Forward Momentum – an Initial Step
So where do we find ourselves in this interesting dilemma? On the one hand, the providers of the capabilities have differing internal views of the benefits, needs, and possibly the digital skill requirements they need for transitioning to an Industry 4.0 environment, while on the other hand it would seem for those that have taken a step forward that scaling, operationalizing, and maximizing benefits of the capabilities are a challenge.
Clarity is necessary. That is why we caught up with a few of the senior managers from EAD (Engineering, Automation and Design) to discuss their views on how to bring clarity via the front-end business case of an Industry 4.0 automation and digitization journey. EAD is a US headquartered engineering, consulting and project management services firm with over 20 years of experience advising global clients in the pharmaceutical, bio-processing, chemical manufacturing, food, and parcel / logistics industries. They specialize in working with clients that operate 24/7/365 and demand a high level of quality, performance, and validation in every project.
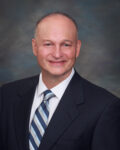
Mark Durica, an Engineering Controls Manager for EAD’s Northeast US office with over 20 years of experience in pharmaceutical industry batch processes, says most clients can benefit from an automation opportunity assessment. “What’s important here is understanding the level of knowledge and sophistication the customer may have. There are some clients that are brand new to the table so you have to start with the basics about what automation can do. Others [clients] already know this so you are looking more at what their particular needs are for project ideas. If they’re looking for project ideas, you can do something called opportunity assessments, where you go into a facility and you talk with operations, the financial people, maintenance people, safety people, and you discuss what are your hassles as it pertains to your process. And that’s where you can find a lot of the opportunities.” Those opportunities might range from a valve that isn’t working correctly to a better method for a temperature control system to operate, or even to looking at energy recovery in an automated way. Understanding replacement options and why systems are set to “manual” all the time instead of running in automatic are all part of the up-front assessment. “You are talking about hassles and opportunities on the OPEX front,” says Durica, “on the capital front, they [clients] pretty much have an idea of what they are trying to accomplish.” By beginning an engagement on the front end, EAD helps clients define project cost estimates and minimize risk. One of the outcomes of an opportunity assessment may even be a vertical slice, in which a virtual prototyping approach is taken to give clients an idea of what they could be deploying. Durica says clients may not always have a good understanding of their options or of the impact that migrating to newer automated systems may have on their businesses, and so this approach provides them with a way to experience the look and feel of automating a system before making a commitment.
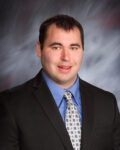
Sean Kendle is a Controls Engineering Manager for EAD’s Omaha, Nebraska office. He has a breadth of expertise in controls automation, including network design, control panel design, programming, HMIs (Human Machine Interface), commissioning and start-up, and remote-control systems. He also has years of experience developing studies that help clients learn about what’s possible with automation. Kendle echoes Durica’s view on the starting point for an automation journey. His clients usually know where they want to go, but find that figuring out how to get there is a challenge.
Not only does the opportunity assessment help confirm project cost budgets, which both engineers agree is important to the overall success of an automation deployment, but it also allows for a reality check on timelines. “Is it realistic? The timeline our clients are shooting for? We can help them with that. Or maybe there are multiple steps to get to the end goal as well. We can help bring those options. And that’s what it’s really about upfront – options,” says Durica.
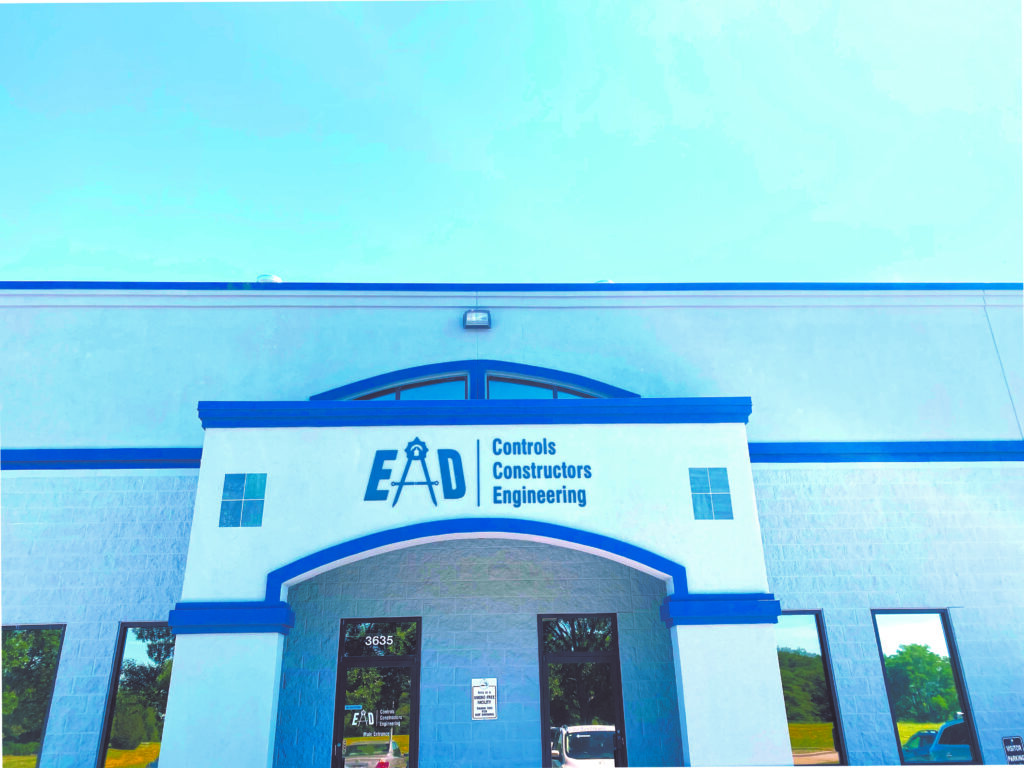
Benefits and Payback
The COVID-19 pandemic brought sweeping changes to the manufacturing industry, pushing manufacturers to rely more on automation to ensure their long-term economic success. As workforces were unable to work due to government-issued lockdowns, manufacturers had to adapt automated processes to avoid foreclosures. So, there are already partial capabilities in place that have not been scaled to end-to-end solutions. Industry 4.0 is about scaling these in such a way that all platforms are integrated through the exchange of digitized information. Automation broadens the opportunities for this digital exchange.
According to Durica, manufacturers and other businesses primarily benefit from automation due to the increases in revenue that result from improvements in process efficiencies and product quality, and the reductions in staffing costs. Automation even makes it easier for manufacturers to ensure their regulatory requirements are met from a traceability and data integrity perspective. “The expectation is that products are made pretty much the same way all the time, and that critical alarms are monitored to make sure nothing goes out of spec during the batch process, in particular. And that helps reduce the documentation load (which is an improvement) from the past where everything was on paper or in log books and such. So, you have better data integrity, and faster processing of the post batch to release it.” Kendle agrees adding, “A lot of companies are struggling to find skilled labor right now. We can help them automate some of their processes to eliminate that need. We can program something to react a lot quicker than a human ever could, and in the correct way.”
Automating the capture of the digital information can help with early detection of out of specification trends and improve troubleshooting capabilities – whereby the data is captured as a function of time and a function of the process and is able to be fed into either an HMI or an analytic tool that provides prognostics information. Startups after “upsets” become less burdensome, and startup sequencing required for a line can be optimized.
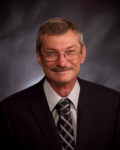
David Read, a Senior Controls Engineer for EAD’s Omaha Office, is responsible for signing off on the design of the firm’s automation processes and drawings. He has been with EAD over 10 years now, and sees similar drivers for automation. But he cautions that automation isn’t just about replacing people. “The majority of what I’m seeing is that manufacturers want to increase productivity and efficiency, and a lot of times automation makes the operators’ jobs a lot easier than they were.” Operators often offer the best source of feedback on automation opportunities because they are able and willing to point out exactly what makes their job a hassle – and in many cases they haven’t been listened to in the past, meaning they have had to deal with long standing issues that go on unaddressed. Kendle says that operators are the best contacts for the best ideas since they have first-hand knowledge of what works and what doesn’t on the plant floor. Read agrees, saying that after making improvements in operators’ jobs, “in a lot of instances, the operators actually get paid more because they now have a higher skilled position after the automation.”
But it’s not only operators who are positively impacted by automation. Maintenance teams also reap benefits. Maintenance teams have more information than ever before, as real-time performance notifications and trend data from machines or the machine’s awareness that it is time for maintenance or preventive maintenance to be scheduled get sent from digitally connected machines. Keeping the lines running without an unplanned shutdown is the goal. Read says, “Time is money right?” Automation can enable better preventive maintenance scheduling. “Take a motor, for instance. If you put a vibration sensor on there, it can warn you that this motor, these bearings are getting ready to go out, and it is going to need to be serviced soon. That gives the maintenance department the ability to say, ‘on this next downtime we need to change this motor or gear box.’ Depending on how deep a company wants to go, you can monitor when you have air leaks to have the ability to determine when a valve is getting ready to fail.” Advanced data analytics can allow for predictive failure horizons, providing recommended windows for change out of parts, or even enabling decisions on types of prevention to prolong life of the equipment.
All three engineers agree that the benefits horizon is about three years for most automation deployment programs, and anything inside of three years is generally considered a bigger win. The lifespan for deployed automation equipment has traditionally been upwards of 20 years. However, some benefits are driven by regulatory and safety requirements, which are sometimes mandated and don’t necessarily need a payback. “You know there’s safety. In Omaha we do a lot of safety projects, “says Kendle, “there is a lot of money, a lot of costs associated with injury or an accident so … we can quantify (that) one accident or one injury is going to cost you on average this much. It’s easy to quantify. There’s actually a risk there…to justify spending a little bit of money on a safety system, or safety studies.”
Data acquisition through automation allows for real-time metrics in terms of throughput, uptime and quality. “With automation you can get that real-time data,” says Read, “and you can see how many pieces and parts have come out of that system throughout the day.” This leads to better information on why lines went down, as well as more accurate insight on the production rates of the lines. As a result, quality metrics like waste can be easily measured by comparing the raw materials used versus the theoretical requirements.
Measuring the Results
Obviously, measuring how well the benefits of automation are realized may also be challenging. Referring to how he measures the results of his work automating systems for food manufacturers, Kendle says, “Up-time and pounds, that’s what I see. The amount of time the line is actually producing, that’s an easy one, and pounds produced.” Mark Durica outlines other measures as well, saying some businesses look at key quality measures such as tracking the amount of rework needed per month. Utility bills provide another easy measure to identify the amount of energy consumed per pound of product produced. Many clients also track quality incidents. According to Durica, “(Clients) can easily track what they call corrective actions-preventive actions (CAPAs). If something happens out of quality, it needs to be investigated.” He says a lot of projects are born out of the CAPAs analysis such as when a company identifies a type of “upset” and then determines the best preventative approach, causing CAPAs to go away.
Right Time Right Now
With the advent of Industry 4.0, a new horizon of opportunity is upon us. Durica summarizes the impact of automation on manufacturing systems with a few words of advice: “Use resources to maximize production. It’s about efficiency. Waste and scrap is energy loss. Higher efficiency brought by automation is good for the environment.
It’s good for people’s safety. Also good for energy conservation, a reduction of waste and scrap that might need to be landfilled. If you are operating a plant more efficiently you are definitely helping out those aspects.”